PEEK is a high-temperature resistant, high-performance thermoplastic special engineering plastic. It has good mechanical properties and chemical resistance, abrasion resistance, hydrolysis resistance, and other properties. So what are the advantages of PEEK material products?
Self-lubricating has a low coefficient of friction, can achieve oil-free lubrication and can work for a long time in oil, water, steam, weak acid and alkali, and other media.
Ease of machining Parts can be directly machined by injection molding. Post-processing such as turning, milling, drilling, tapping, bonding, and ultrasonic welding can be performed.
Low-smoke and environmentally friendly The amount of smoke and toxic gas are extremely low when burning.
High-temperature resistance US UL certification The long-term use temperature is 260 ℃; even when it reaches 300 ℃, it can still maintain good mechanical function and wear resistance. In many harsh use environments such as high temperature, high load, and strong corrosion, PEEK compound, And its composite materials have good wear resistance.
High strength has mechanical strength in plastics. It also has high rigidity and surface hardness.
Corrosion resistance is insoluble in common solvents and has good corrosion resistance to various organic and inorganic chemical reagents.
Resistant to hydrolysis When soaked in steam at over 250°C or high-pressure water, PEEK products can still work continuously for thousands of hours without significant functional decline.
The electrical function can maintain stable and excellent electrical function in a wide temperature and frequency range.
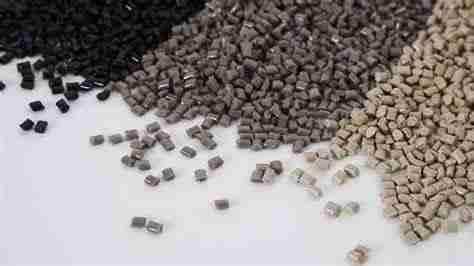
Learn about the benefits of PEEK materials.
The advantages of PEEK material properties:
PEEK: the gold material in the injection molding industry
PEEK, the Chinese name is polyetheretherketone, is called together with polyphenylene ether (PPS), polysulfone (PSU), polyacrylonitrile (PI), polyacrylate (PAR), and LCD screen polymer (LCP). 6 special engineering plastics.
Peek polyether ether ketone is a special engineering plastic with excellent properties such as heat resistance, self-lubricating bearing, easy production and processing, and high impact toughness. It can be manufactured and processed into various mechanical parts. The advantages are as follows:
1: Corrosion resistance and aging resistance;
2: Anti-solubility;
3: High temperature and high-frequency DC performance standards;
4: Both ductility and stiffness;
5: Specifications specify high-precision standards;
6: Irradiance resistance, wear resistance, and corrosion resistance standards;
7: It is resistant to hydrolysis reaction and can still maintain excellent characteristics under ultra-high pressure;
8: Lightweight replacement of metal materials for optical fiber components;
9: Good anti-wear, anti-static insulation performance;
10: The impact toughness is specified for high components;
11: Low dust and toxic gas discharge.
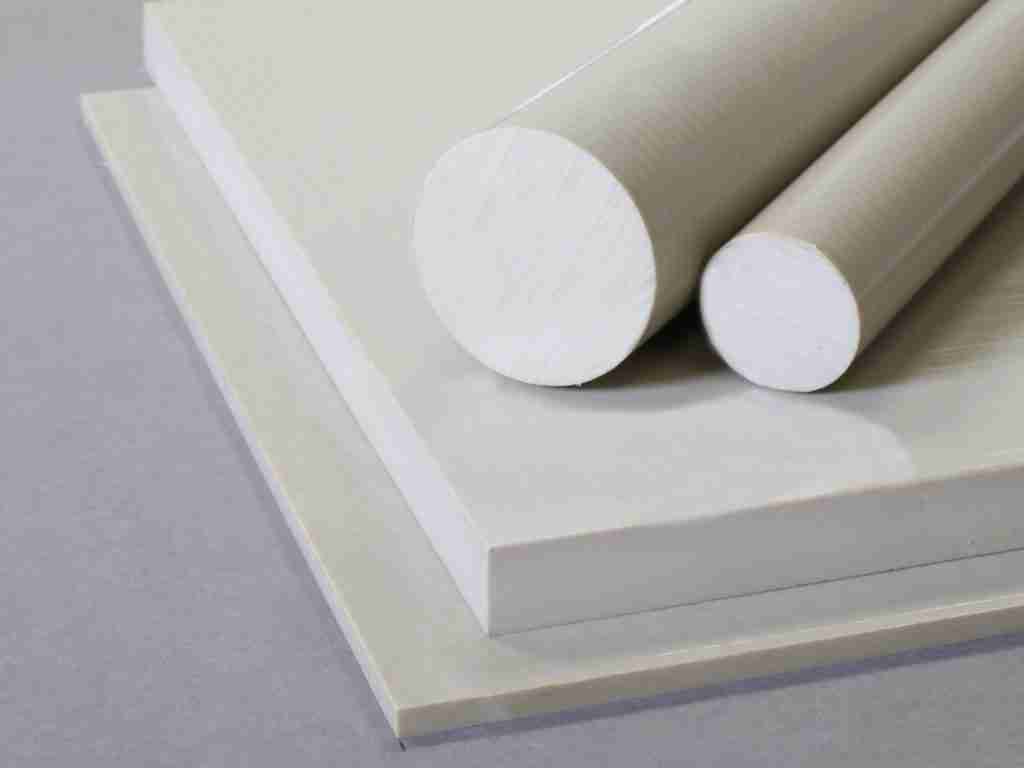
Understanding PEEK Material Properties
The performance of PEEK material is mainly manifested in the following aspects:
1. High-temperature resistance
PEEK has a high glass transition temperature and melting point (334°C), which is one of the reasons why it can be used reliably in applications requiring heat resistance. Its load thermal deformation temperature is as high as 316 °C, and the continuous use temperature is 260 °C.
2. Mechanical properties
PEEK is a plastic with a balance of toughness and rigidity. In particular, its excellent fatigue resistance to alternating stress is outstanding among all plastics, comparable to alloy materials.
3. Self-lubricating
PEEK has good sliding properties in all plastics and is suitable for applications where low coefficient of friction and wear resistance are strictly required. In particular, the self-lubricating performance of PEEK modified with carbon fiber and graphite in a certain proportion is better.
4. Chemical resistance (corrosion resistance)
PEEK has good chemical resistance. In common chemicals, only concentrated sulfuric acid can dissolve or destroy it, and its corrosion resistance is similar to that of nickel steel.
5. Flame retardancy
PEEK is a very stable polymer, and a 1.45mm thick sample can achieve a high flame retardant standard without any flame retardant.
6. Peel resistance
PEEK is resistant to peeling so it can be made into very thin or magnet wire and used in harsh conditions.
7. Fatigue resistance
PEEK has better fatigue resistance than all resins.
8. Radiation resistance
The ability to resist gamma radiation is very strong, surpassing that of polystyrene, which has better radiation resistance among general-purpose resins. It can be made into high-performance wires that maintain good insulation when the gamma irradiation dose reaches 1100Mrad.
9. Hydrolysis resistance
PEEK and its composite materials are not chemically affected by water and high-pressure water vapor. Products made of this material can maintain their properties under continuous use in high-temperature and high-pressure water.
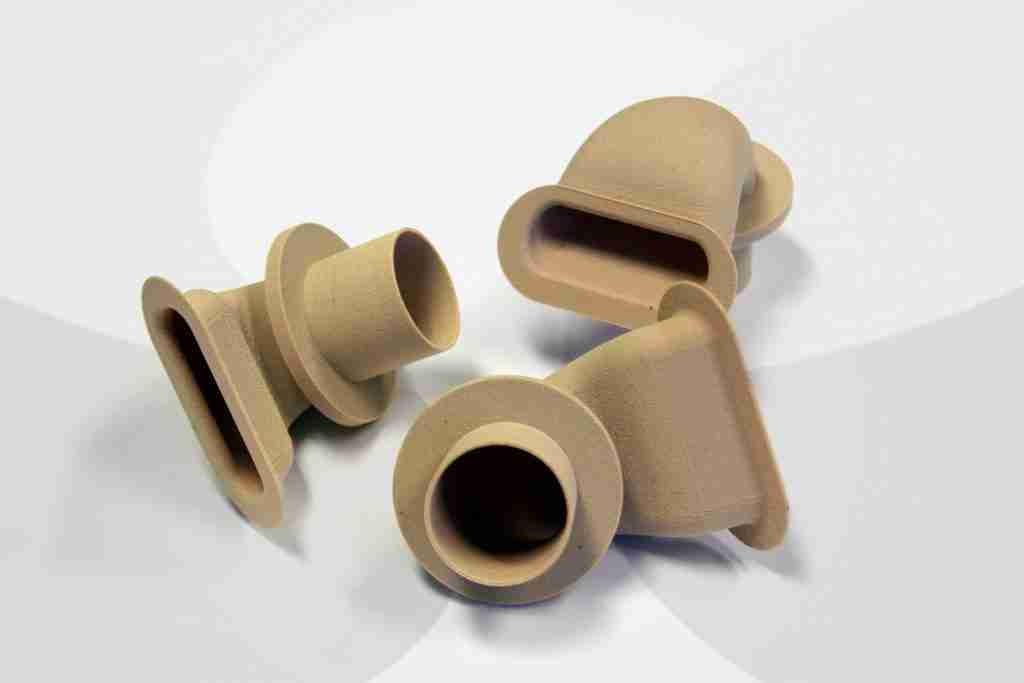
The main application of PEEK material
PEEK polyetheretherketone is a special engineering plastic with excellent properties such as high-temperature resistance, self-lubricating, easy processing, and high mechanical strength. So, where are PEEk materials mainly used? The main fields are automobiles, etc. (including aviation). The transportation market accounts for about 50% of PEEK resin consumption, semiconductor manufacturing equipment accounts for 20%, general mechanical parts products such as compressor valves account for 20%, and other markets such as medical equipment and analytical instruments account for 10%.
1. Transportation machinery such as automobiles
The growth of PEEK resin in the European market, especially the rapid growth of the auto parts market, especially the parts around the engine, transmission parts, steering parts, etc., have chosen PEEK plastics instead of some traditional high-priced metals as manufacturing materials. Demand for PEEK resins will continue to grow as the automotive industry adapts to miniaturization, lightweight and cost reduction. A European model has 44 parts that use PEEK plastic instead of traditional metal products.
2. The field of IT manufacturing
Semiconductor manufacturing and the electrical and electronic industry are expected to be another growth point for PEEK resin applications. In the semiconductor industry, to achieve high functionality and low cost, the size of the silicon wafer is required to be larger, and the manufacturing technology is better. Special requirements will be where PEEK resins come into play.
3. The field of office machinery parts
For the separation claws, special heat-resistant bearings, chains, gears, etc., of copiers, when PEEK resin is used instead of metal as their material, the parts can be lightweight, fatigue-resistant, and can be lubricated without oil.
4. The field of wire coating
PEEK coating has good flame retardancy; without any flame retardant, its flame retardant level can reach UL94 V-0. PEEK resin also has the advantages of peel resistance and radiation resistance (109 rad), so it is used in special wires in military and nuclear energy and other related fields.
Elimold is a production factory integrating mold design and manufacturing and injection molding production. The company has made great achievements in digital electronic injection molding parts, small home appliance shell injection molding parts, sports equipment plastic parts, and adult products plastic accessories.