Aerospace 3D Printing
At Elimold, we specialize in high-performance 3D printing solutions for aerospace. Using cutting-edge additive manufacturing techniques, we create lightweight, durable, and complex components that enable you to innovate in the air and beyond. Turn your ideas into reality with our expert services. We can meet all your manufacturing needs with precision, speed, and affordability. Get an instant quote now.
Your Aerospace 3D Printing Service Partner
Welcome to explore more possibilities of 3D printing in the aerospace industry with Elimold. We specialize in multi-color 3D printing and manufacturing high-quality 3D printed aerospace parts. Our expertise lies in the precise and efficient manufacturing of custom 3D printed aerospace parts. In fact, we have seen that the applications of 3D printing aerospace are varied and limitless as we meet a large number of needs across the industry. Fortunately, our focused solutions enable companies to revolutionize their production capabilities and turn innovative concepts into reality. Whether producing specialized components, complex geometries or lightweight structures, we are a trusted partner for 3D printing in the aerospace industry.
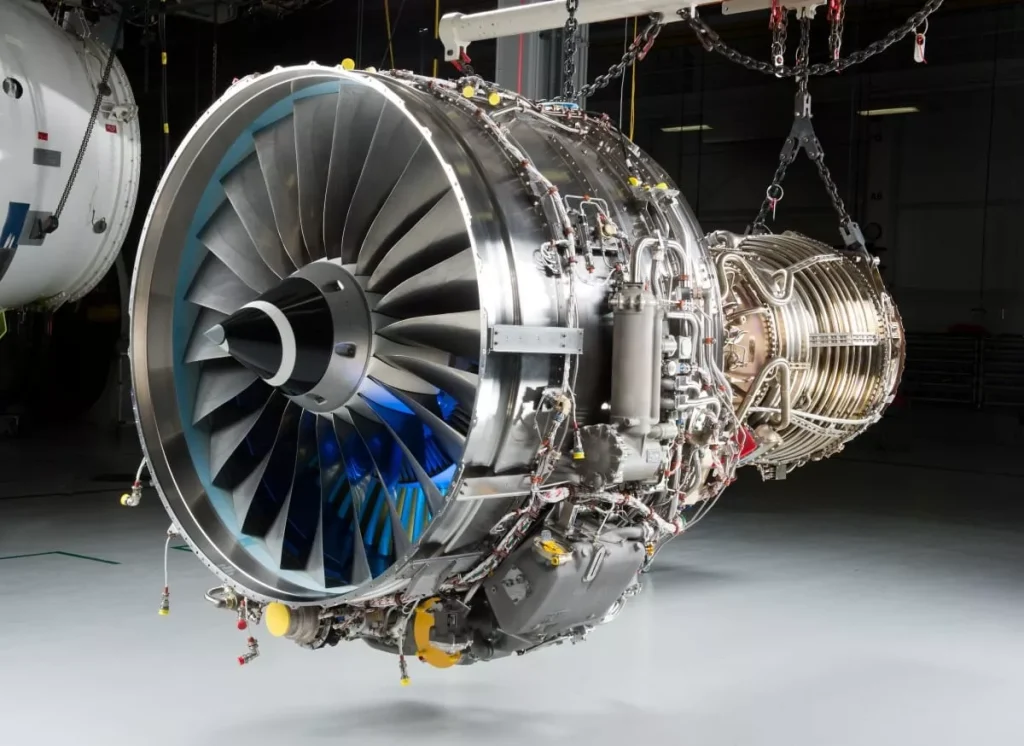
Discover New Opportunities in Aerospace
3D printing technology has become an essential part of aerospace production in the production of custom parts in the aerospace industry. We expect the trend of using additive manufacturing in aerospace to continue to increase. Through close collaboration with customers, Elimold fully understands the challenges that airlines face today. The industry is facing a huge technological transformation related to environmental impact. Additive manufacturing provides aerospace companies with a powerful tool to achieve change. Achieving the net zero carbon emissions commitment requires large-scale innovation, open-minded managers, and the implementation of comprehensive solutions to make aerospace more environmentally friendly. The growing market for high-performance polymers and composites provides an excellent opportunity to manufacture extremely durable end-use parts that are lighter than metal alternatives and still resist heat, pressure, impact, chemicals and the elements.
Industrial 3D Printing for Aerospace Engineering Parts
Due to the cost and risk of developing new aerospace products, designers need to ensure they can implement them right the first time. With industrial 3D printing, you can unlock flexible prototyping for numerous iterations, leaving no room for error. You’ll develop aerospace innovations with unprecedented efficiency, and control your supply chain to produce factory tools in-house, with the potential to significantly reduce product development costs and lead times. Power aerospace engineering from the lab to the sky with Elimold’s proven aerospace industrial 3D printing solutions, whether you need plastic or metal parts. Modernize your production today.
How can Elimold help?
Elimold’s aerospace 3D printing services are a fully integrated solution that accelerates your pace of innovation, getting you to orbit faster than ever before. Produce custom parts in days, not months, and get products to market in months. Develop prototypes and production-grade parts for a wide range of aerospace high-performance products from a single source. Allow your engineers to focus on optimal performance, not manufacturability. Produce the designs you want without having to compromise to fit traditional Design for Additive Manufacturing (DfAM) limitations. Seamlessly transition to mass production by leveraging our global contract manufacturing network or manufacturing in-house with our high-volume 3D printing solutions.
Diverse 3D printing technologies to meet various needs
Fused Deposition Modeling (FDM)
Stereolithography (SLA)
Direct Metal Laser Sintering (DMLS)
Electron Beam Melting (EBM)
PolyJet Printing
Selective Laser Melting (SLM)
Multi Jet Fusion (MJF)
Carbon DLS
Selective Laser Sintering (SLS)
Our Industry-Leading 3D Printing Capabilities
Backed by years of pioneering experience, we offer the industry’s most comprehensive selection of metal and plastic 3D printing technologies and materials for any aerospace application, whether small or large, simple or complex, prototype or production. Our experts work closely with your team on everything from identifying and evaluating 3D printing candidates to exploring design improvements and cost savings.
We support customers in the aerospace industry by offering:
- application and technical expertise at every stage of development and production
- large-format 3D printing for metal parts as large as 31.5 in. x 15.7 in. x 19.7 in. and plastic parts as large as 29 in. x 25 in. x 21 in.
- quality certifications: ISO 9001:2015, AS9100, ITAR registered
- diverse secondary processes like machining and threading and heat-treat options such as standard stress relief or solution and aging
- AS9102 first article inspection report capability
Ready to Innovate Your Aerospace Project with Our 3D Printing Experience & Expertise?
Full range of aerospace 3D printing solutions
Rapid tooling and manufacturing aids for aerospace suppliers of any size
- Reduce overhead and increase efficiency with custom jigs and fixtures.
- Respond to customer demand for more custom products and low-volume orders with rapid tooling.
- Maximize equipment uptime by printing replacement parts on demand.
Rapid prototyping from concept to pre-production
- Bring additive manufacturing capabilities in-house to save time, reduce costs, and keep sensitive intellectual property within your organization.
- Communicate your ideas to customers and suppliers with high-quality prototypes.
- Test and validate components before mass producing aircraft, spacecraft, or parts.
Aerospace 3D Printing End-Use, Replacement, and Custom Parts
- A large library of proprietary high-performance materials for producing parts that meet extreme environmental challenges.
- No waiting or overpaying for tooling. Gain flexibility and take on more non-traditional work by 3D printing parts directly in your factory.
- Replicate or improve existing designs for maintenance, repair, and overhaul of aircraft, helicopters, drones, rockets, rovers, and more.
Quality Assurance in Aerospace: Optical Tomography
High safety requirements for approvals are a major challenge in the aerospace sector. From the raw material to the end product, every flight component must be constantly monitored and must not have any defects.
Elimold uses an optical tomography technology for manufacturing processes and applies it to the manufacturing process of custom parts for aerospace. Parameterizable software allows detailed conclusions to be drawn about the quality of the part layer by layer. In this way, optical tomography verifies repeatability, increases comparability between parts, build jobs and printing systems, and creates the right conditions for cost-effective quality assurance in series production applications.
Why do Aerospace Companies Use Elimold?
Speed and reliability are key during the design, validation, and launch of aerospace components. Our 3D printing services support the industrial manufacturing of intricate and complex geometries to lightweight part designs or reduce the number of components in an assembly.
Advantages of Elimold 3D Printing for the Aerospace Industry:
- Streamlined Certification: Our methodology and process specifications facilitate the certification of aeronautical parts.
- Comprehensive Manufacturing Management: Our system ensures the complete traceability of equipment and raw materials.
- No tooling required.
- Consolidation of assemblies and minimizing the number of parts required.
- Design freedom for complex geometries.
- Enhanced weight efficiency.
- Certified aerospace thermoplastics (FST – FAR 25.853).
- Tailored machine park for aircraft interiors.
Material Options
Plastic Materials
- ABS
- Nylon
- Polycarbonate (PC)
- Polypropylene (PP)
- Silicone
- TPU
- Digital Photopolymer
Metal Materials
- Aluminum
- Cobalt Chrome
- Inconel
- Stainless Steel
- Titanium
Metal 3D Printing Makes Tool-less Production a Reality for the Aerospace Industry
By incorporating metal 3D printing technology into the aerospace custom parts manufacturing process, large complex parts and high-density metal assemblies can be easily manufactured with reduced lead times. The ability to 3D print complex metal parts directly from 3D CAD files and quickly modify them to accommodate design changes provides more opportunities for proving out parts for aerospace applications. Then 3D print the metal parts directly without having to make die casting molds, which increases design flexibility and reduces on-site storage requirements.
Production with metal 3D printing is faster than die casting, and more prototype parts can be produced at one time. Since you can print as many prototypes as you need, there is no limit to the number of prototypes available.
Aerospace applications include castings for complex gearboxes and covers, fuel tanks, transmission housings, parts that require no vent walls, lightweight engine components, and structural hinges. Metal 3D printing systems can also directly batch print small metal parts using MiM powders suitable for aerospace manufacturing.
3D printing of lightweight, strong aircraft components
3D printing technology makes it possible to use material only where it is needed, without having to sacrifice the functionality of the component. By optimizing the topology, engineers have been able to continuously improve the efficiency, durability and resource utilization of components. Additive manufacturing and the geometric freedom it offers are particularly useful in this regard.
With the help of modern software solutions, computers can calculate the load distribution within the component and generate new optimized models based on the data. The end result is 3D-printed aviation components with highly complex geometries and structures. It is often uneconomical to manufacture these components using traditional methods such as CNC milling or CNC turning. This is where additive manufacturing of aviation components comes into play. And additive manufacturing is not restricted by geometry, even in aircraft construction. This enables engineers to fully exploit the design freedom to develop lighter and stronger components.
Application of 3D printing in aerospace
Whether it is to increase performance or aerodynamics, save material or optimize functionality. 3D printed aviation components are used both in cabin interiors and in engine transmissions. In the form of brackets, seat frames or nozzles, additive manufacturing is helping the aviation industry to continuously improve the ecological balance of air traffic and reduce CO2 emissions.
For large projects, there is also an additive solution. With Voxeljet binder jetting technology, detailed investment casting patterns with component lengths of up to 1 meter can be printed. Sand 3D printing can even print component lengths of up to 4 meters. In addition, indirect 3D printing also has the certification and material freedom of metal casting.
Currently, many metals cannot be directly processed by additive or have not yet been approved for use in aviation. In contrast, additive molds and patterns can be used to process all castable alloys. Since the material properties are known, the cast components can be directly integrated into the production line.
Manufacturing aircraft engine components with industrial 3D printing
Building engines and turbines means meeting various challenges, such as optimizing volume, performance and environmental friendliness. In these areas, metal 3D printing can make a significant contribution. It enables the production of engines with complex geometries, defined aerodynamics and fluid dynamics, and lightweight structures with up to 60% lighter individual parts. Processing superalloys with 3D printing is also more cost-effective, as material usage is lower. The result is significantly less environmental pollution over the entire service life of the aircraft. Components made from a single piece are also more resilient and less susceptible to damage.
Manufacturing components and structures with industrial 3D printing
Reducing cost drivers. This is a key factor in making structural parts more efficient for the aviation industry. Digital manufacturing processes offer a wide range of opportunities. With additive manufacturing, several parts can be combined into one component, thus eliminating production steps such as assembly. The current capital-intensive storage of spare parts will also be eliminated. Parts are only produced when they are needed, without any prior processing. In addition, additively manufactured structural parts are relatively light and help balance the aircraft’s CO2 emissions.
3D Printing Aircraft Components and Structures
Additive manufacturing applications in the aerospace industry are driving lightweight construction projects in particular. Optimizing components in the interior or in aircraft engines can reduce material and fuel consumption and thus reduce CO2 emissions. Furthermore, 3D printing offers the aerospace industry the possibility of monolithic component consolidation, which can simplify complex component groups and streamline production lines and steps.
3D printed models are particularly advantageous for investment casting. Investment casting is a fully certified additive manufacturing process for the aerospace industry. Combining investment casting and 3D printing in aircraft part manufacturing therefore eliminates any time-consuming certification processes. As a result, even small and medium-sized series of prototypes, spare parts and product design iterations can be ready for use in record time.
Aerospace 3D Printing Applications
Our 3D printing processes are most leveraged throughout the prototyping process for aerospace applications but can also be used for part consolidation and end-use production. 3D printing is often used for varied aerospace components including:
- Jet engines
- Fixtures and jigs
- Brackets
- Turbine blades
- Ducting systems
- Engine exhaust systems
- Heat exchangers
- Manifolds
- Turbo pumps
- Liquid and gas flow components
- Fuel nozzles
- Conformal cooling channels
The Future of Additive Manufacturing in the Aerospace Industry
The U.S. and Canada are witnessing an increasing adoption of 3D printing technologies in the aerospace industry. As a result, the North American region as a whole is projected to be the largest market for aerospace 3D printing. The increased demand for lightweight aircraft components integrates perfectly with the 3D printing industry as a whole in general. The introduction of Onyx FR-A and Carbon Fiber FR-A is only the beginning of where these applications are headed. We are expecting to see more applications for additive manufacturing because these parts are high quality, and the engineers can make changes quickly in accordance to customer requests. The accuracy, profitability, and inspection processes of 3D printing continues to increase with artificial intelligence, new printers, and improved software. As a result, it makes sense for more engineering and contract manufacturing companies to begin integrating this technology into their aerospace industry workflows.
Next Generation 3D Printed Aerospace Parts
Next generation aerospace 3D printed parts are definitely lighter, more durable and higher performance. Industries such as aviation place increasingly stringent demands on the chemical, physical and mechanical properties of the parts used. Parts must not only meet extremely high safety requirements, but also have a long service life. This is why more and more of these parts are produced using additive manufacturing technology.
Heat-resistant and corrosion-resistant 3D printed parts are the first choice for demanding parts in the aviation industry. The materials used for the next generation of 3D printing from Elimold must have high strength and oxidation resistance, which can make the products run at high temperatures and become indispensable products for aerospace parts. In particular, the excellent performance characteristics of parts made of these materials in extreme environments. In addition, our special metal 3D printing technology is also the best choice for the next generation of 3D printed aerospace engine parts. When it comes to functional prototypes and spare parts production, Elimold’s extensive portfolio of stainless steel alloys can meet your requirements.
Ready to Get Your Project Off the Ground?
Speak to an aerospace, defense, and space industry 3D printing expert today! Our team is standing by, ready to help answer questions or get started on a quote for your project.