Vapor Smoothing Services
Post-processing 3D printed parts with vapor smoothing allows parts to become watertight, stronger, and smoother. This is possible without the degradation of mechanical properties. Post vapor smoothing, you can expect a surface finish extremely close to injection molding.
Vapor Smoothing for 3D Printing
Fully automated surface treatment technology smoothes and seals the surface of 3D-printed polymer parts. Achieve a surface finish with an injection-molded look and feel.
The process is non-line-of-sight, so complex geometries and cavities of thermoplastic parts can be smoothed without degrading mechanical properties. Steam smoothing can create a polished, consistent finish on your 3D parts. Traditional injection molding for mass production takes parts directly from the mold with a mirror or textured finish. No post-processing is required, and the parts can be packaged and shipped to their destination after cooling. Molders use polishing techniques with brushes, felt, stones, and other tools to achieve this complete finish.
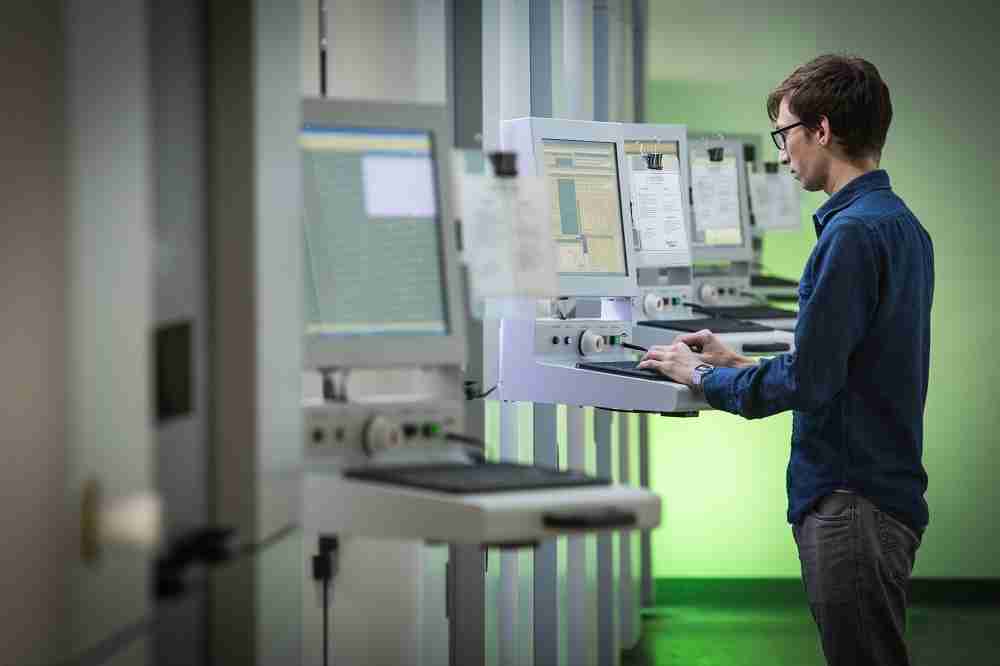
Steam Smooth 3D Printed Parts
3D printing is one of the best ways to get products in small batches. However, plastic 3D printing often involves an important trade-off: rough-surfaced parts. Powder bed fusion processes such as Selective Laser Sintering (SLS) and HP Multi Jet Fusion (MJF) leave a matte sugar cube-like surface finish. Fused Deposition Modeling (FDM) shows different layer lines. In the past, post-treatment surface finishes such as abrasive media tumbling, hand finishing, or coating have slightly improved the surface finish of 3D printed parts. Engineers may opt for other processes entirely, such as injection molding, CNC machining, or polyurethane casting.
With the introduction of chemical vapor smoothing, a technique that smoothes 3D printed surfaces and improves mechanical properties by vaporizing a solvent, 3D printed plastics are now more suitable for low-volume production than ever. Chemical vapor smoothing works with most 3D-printed polymers and elastomers.
Performance Enhancement
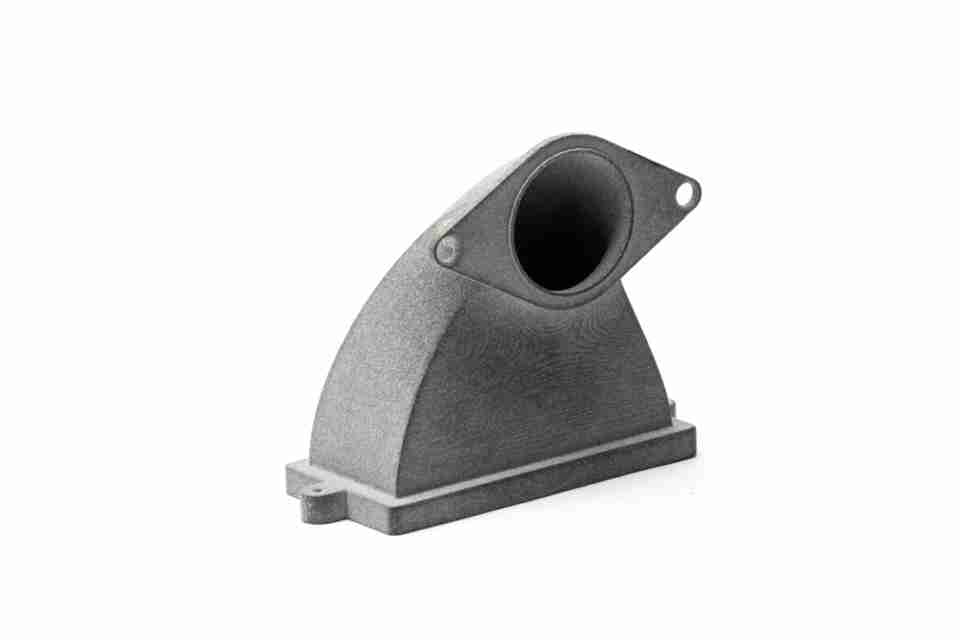
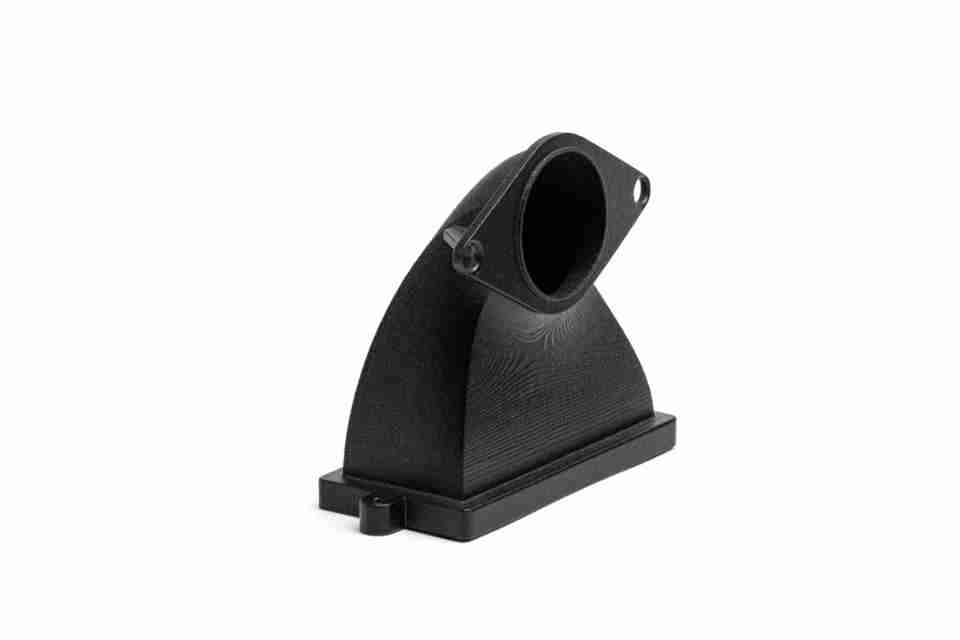
Increased Mechanical Properties
Due to the removal of surface porosity, extensive testing demonstrates that vapor smoothed demonstrated no loss in Ultimate Tensile Strength (UTS) with an increase in Elongation at Break (EAB).
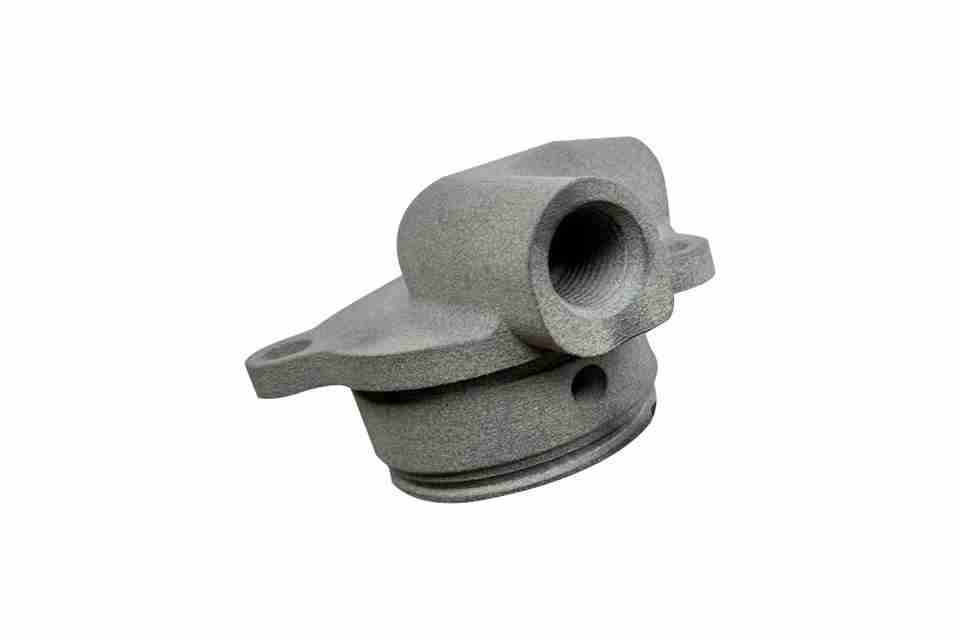
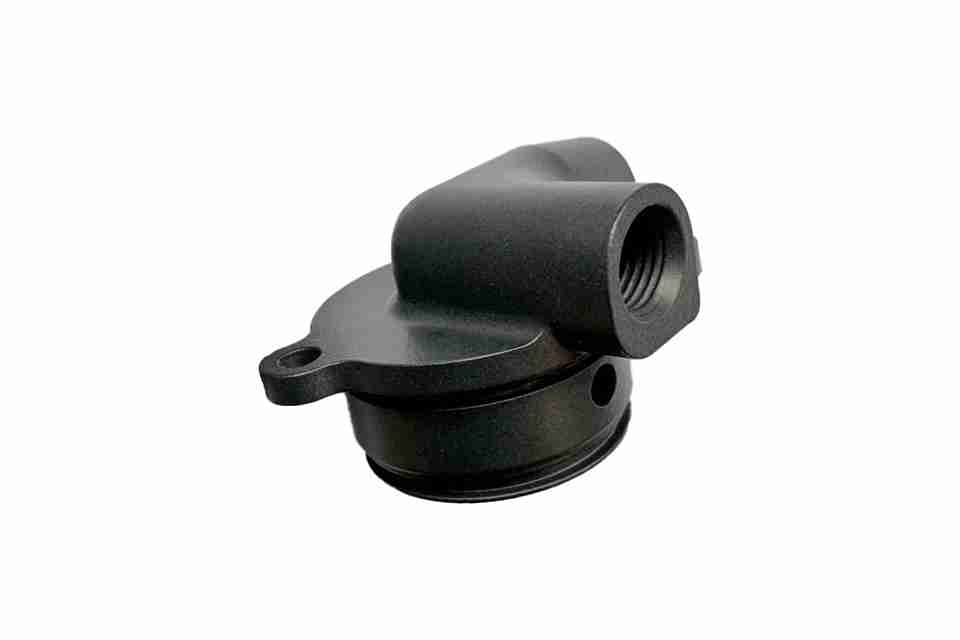
Injection Molding-Like Surface
Using a series of predefined parameters, this process achieves for the first time a surface finish that matches injection molding techniques with an RA of less than 1 micron.
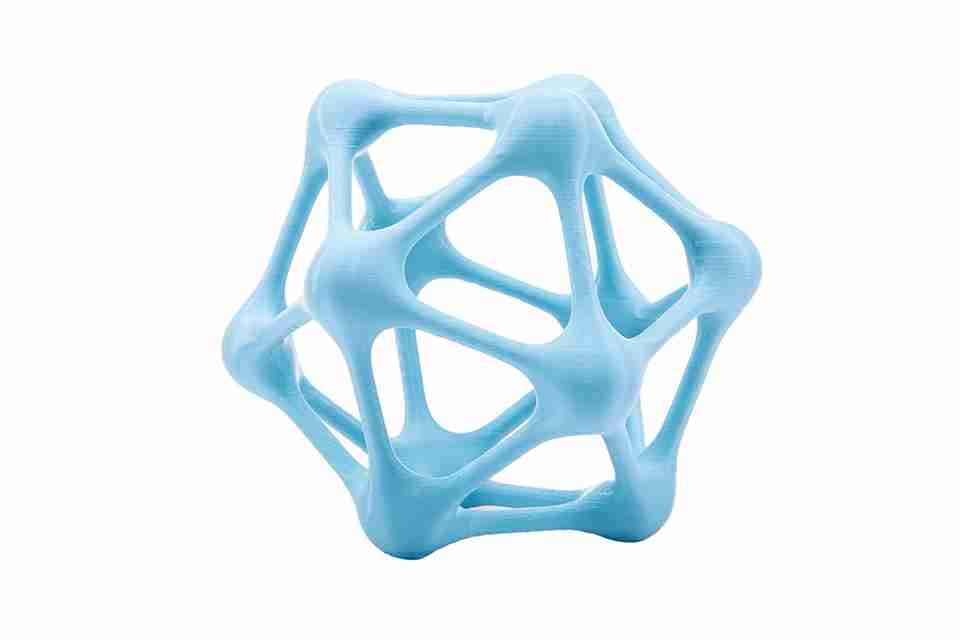
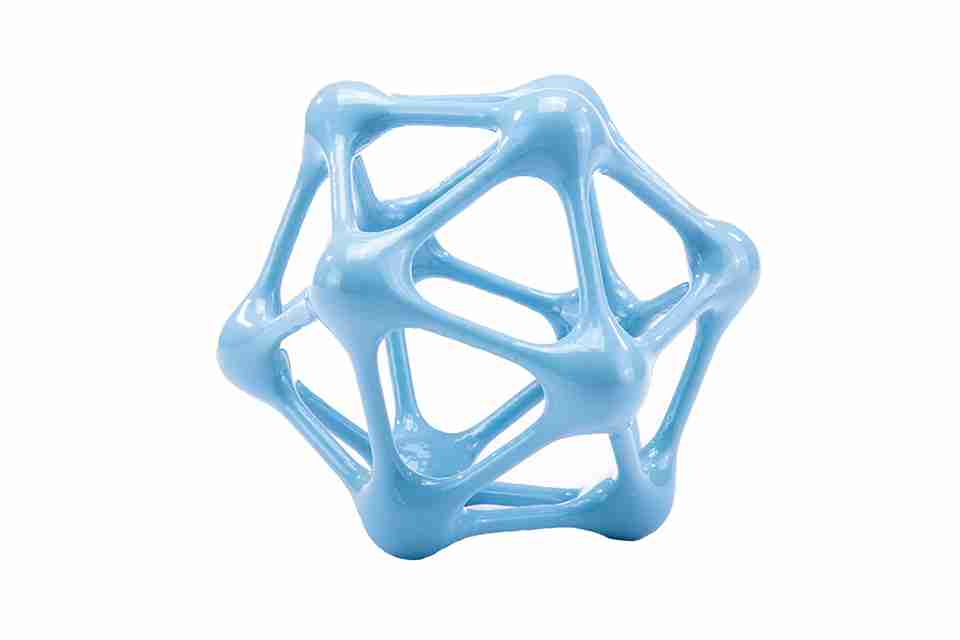
Dimensional Accuracy
The process does not degrade the mechanical properties of the parts. After the treatment, parts exhibit no more than a 0.4%-dimensional change, irrespective of the desired finish level.
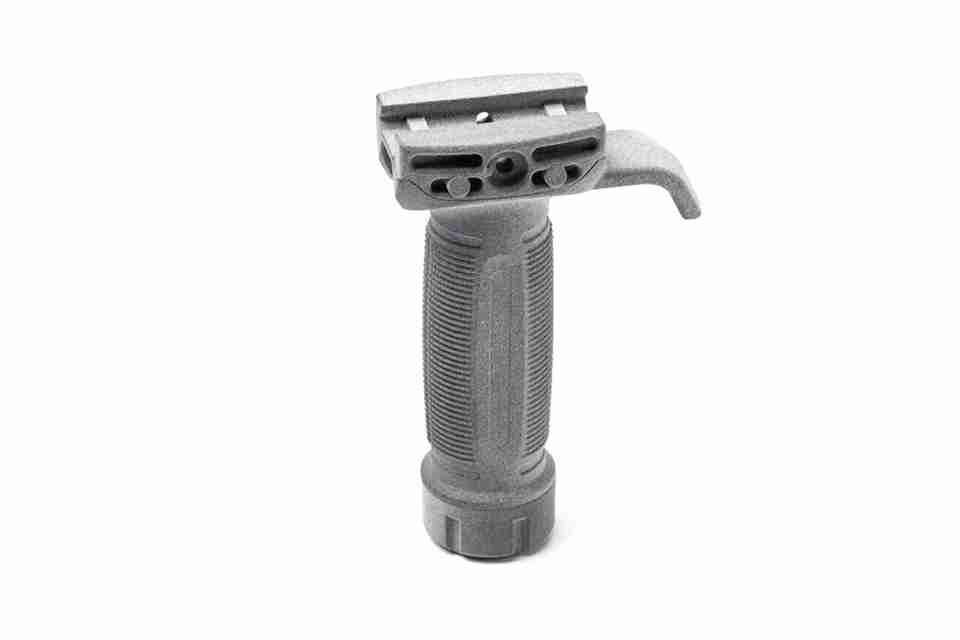
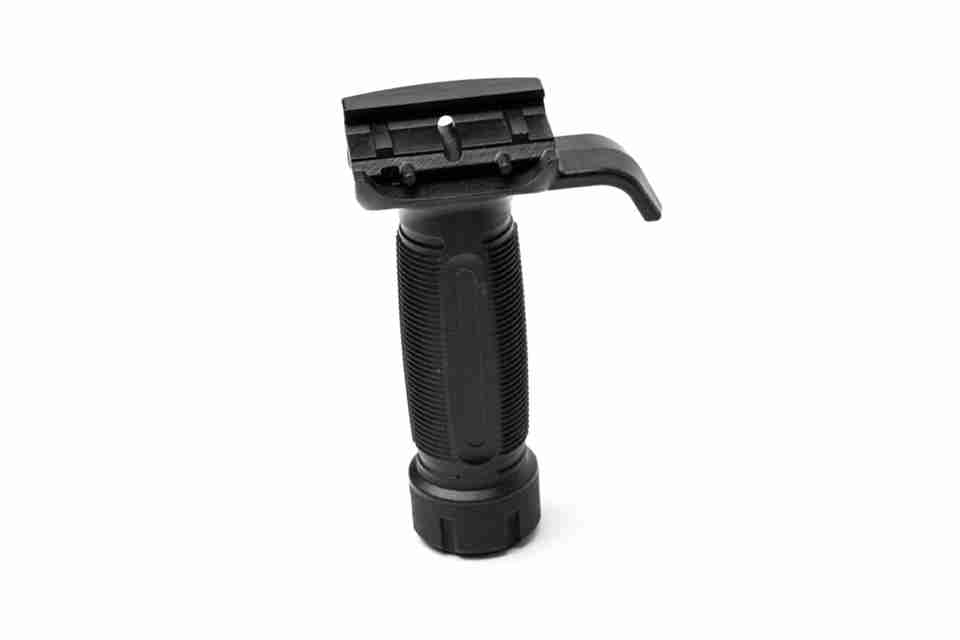
Seals Against Liquid & Gas Intake
The treatment completely seals the surface, eliminating liquid or gas intake. As a result, parts become watertight and airtight.
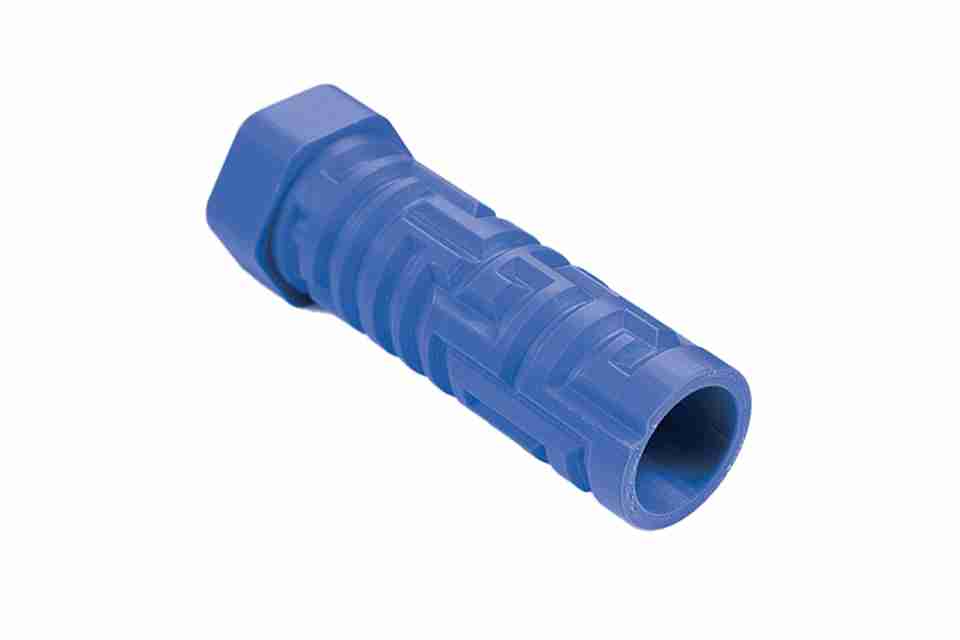
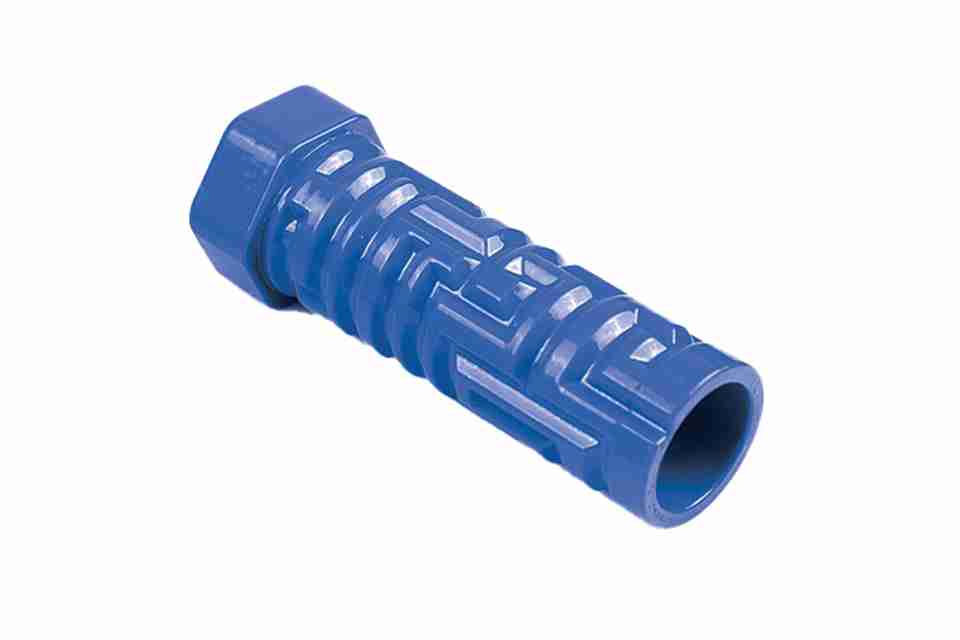
Enhances Colour
Vapor smoothing enhances the color consistency and hue of the colored part. Additionally, parts with color, such as HP MJF 580 parts, do not bleed in PostPro 3D machines.
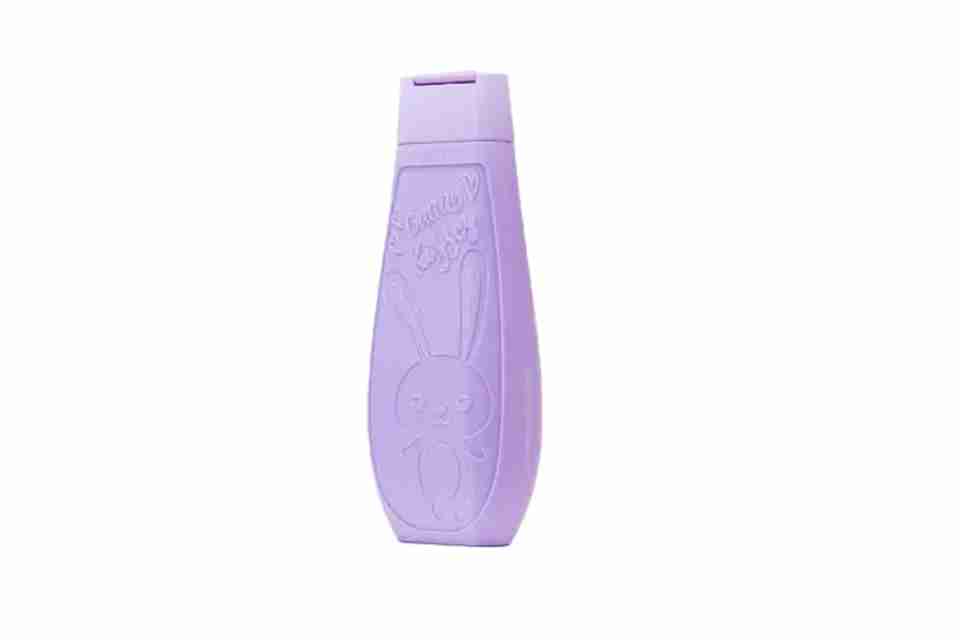
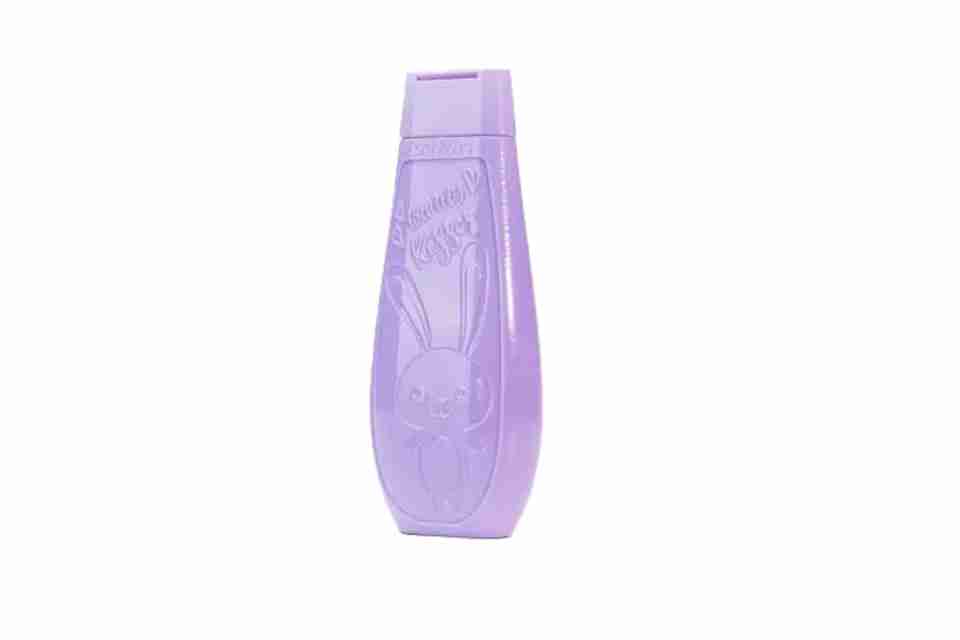
Reduction in Bacteria Growth
Tests have shown the reduction of bacteria growth and attachment on parts that have been chemically vaporing smoothed.
Vapor Smoothing Creates a Polished Part In Seconds
Vapor Smoothing is a fast, effective way to achieve a smooth finish for your 3D Printed Objects. By using the Vapor Smoothing System, 3D printed parts can be finished to a fine smoothness without losing the detail of the original printed part.
- Consistent, uniform results to every part that is vapor smoothed.
- Significantly reduced processing times from hours to minutes.
- Smoothing of parts with complex geometries and intricate angles.
- Easy removal of small layer lines.
- Smoothing of most FDM thermoplastics, including ABS and ASA.
- Elimination of the use of flammable solvents like Acetone and THF.
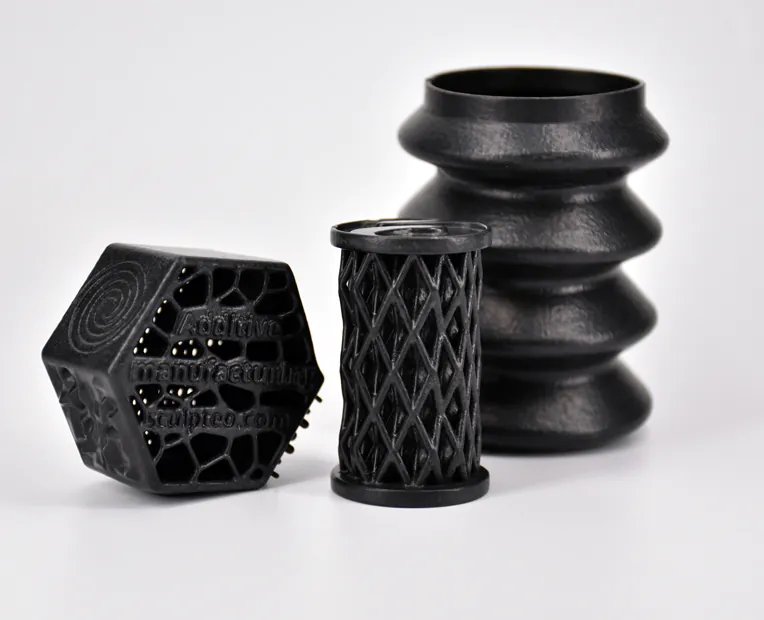
Vapor Smoothing Design Guidelines for Printed Parts
Maximum part size | 10.6 in. x 12.6 in. x 16.0 in. (269mm x 304mm x 406mm) |
Tolerances | For well-designed parts, tolerances of ±0.010 in. (0.25mm) plus 0.1% of nominal length can typically be achieved. Note that tolerances may change depending on part geometry. |
Wall thickness |
|
Minimum feature size | 0.03 in. (0.762mm) |
Part features | Ideally, the part would have a through hole with a minimum diameter of 0.04 in. (1mm) or an exterior wall with a thickness between 0.04 in. (1mm) and 0.20 in. (5.1mm) so that the part can be easily hung from a rack. We can still smooth almost any part, regardless of its features, but we may have to add a small sacrificial feature that would be removed after smoothing, leaving a small ~2m diameter non-smoothed mark on the part’s surface. |
Warpage | Larger part sizes (>7 in.) and parts with thin features are the most susceptible to warp. We recommend maintaining a uniform thickness of 0.125 in. (3.175mm) to ensure stability. |
Post-process finishing | Vapor smoothing can be combined with additional post-processing steps such as tapped or threaded inserts or painting. |
What 3D Printed Materials Can Be Vapor Smoothed?
The following table lists compatible materials that can be chemically vapor smoothed by Elimold, including materials that may require manual review.
Materials | Process |
---|---|
Nylon 12 | SLS, HP MJF |
Nylon 12, Glass Bead | SLS, HP MJF |
Nylon 11 | HP MJF |
Thermoplastic Urethane, TPU 88A | HP MJF |
Polypropylene (PP) | HP MJF |
Nylon 11 EX | SLS |
Nylon 12, Carbon-Filled (CF) | SLS |
Nylon 12, Aluminum-Filled (AF) | SLS |
Nylon 12, Mineral-Filled (HST) | SLS |
ABS-M30 (6 colors) | FDM |
ABS-ESD7 | FDM |
ABS-M30i | FDM |
ABSi | FDM |
ASA (10 colors) | FDM |
Nylon 12 | FDM |
Polycarbonate (PC) | FDM |
PC-ABS | FDM |
PC-ISO | FDM |
Get an instant quote on your 3D printing design.
We invite you to send us some of your sample 3D printed parts and we will vapor smooth them. You will see first-hand how well the vapor polishing process works. Simplify your 3D print post processing!
What is Vapor Smoothing?
Vapor Smoothing is a post-processing technique used in 3D printing to improve the surface finish of printed parts. The process uses the heat and condensation of steam to smooth and level the surface of the part, thereby reducing common defects in the printing process.
Vapor Smoothing is performed in a special sealed chamber equipped with a heating and steam supply system. The 3D printed component is placed in this chamber. Then, vapor generated by the heating of the solvent is injected into the chamber. The vapor condenses on the surface of the part, a phenomenon that causes the surface of the material to partially soften and smooth it through surface tension. This effect smoothes and evens out the characteristic porous surface caused by multi-jet fusion printing, resulting in a smooth and uniform surface. The processing time depends on the material, component size and the desired surface finish.
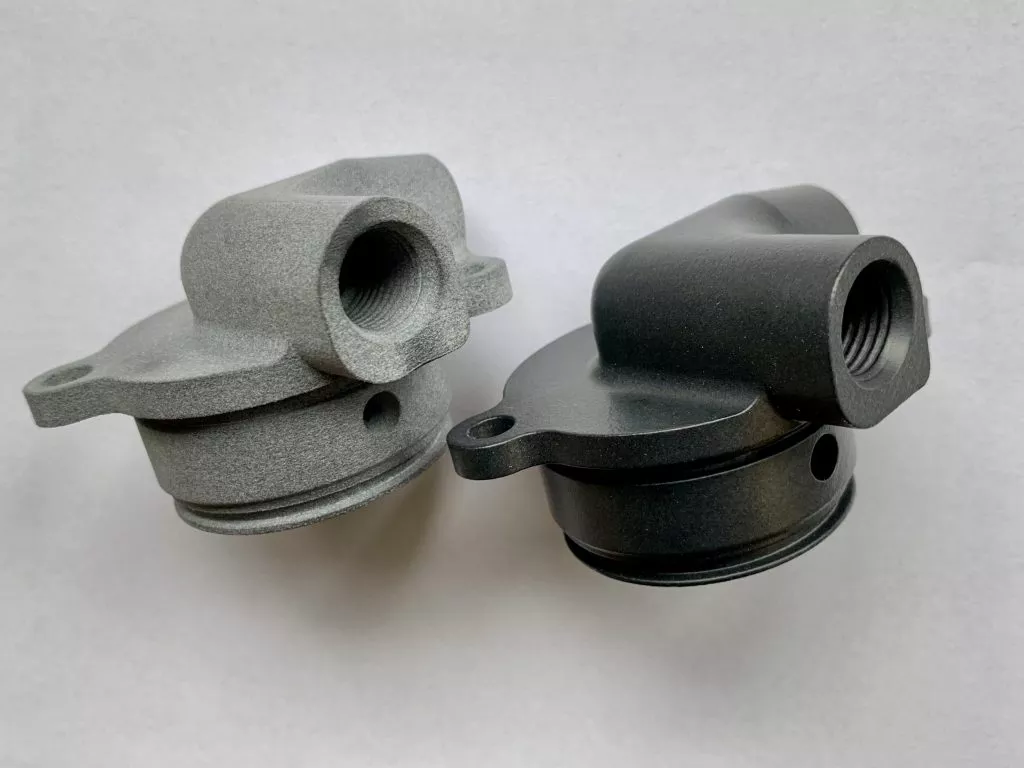
Benefits of Vapor Smoothing 3D Printing
Vapor-smoothed parts improve the appearance and rival an injection-molded surface finish. The surface roughness of standard SLS parts is typically greater than 250uin Ra but can be improved to below 125uin Ra and as low as 40uin Ra by chemical vapor polishing. Chemical vapor smoothing can improve material surface by 800%-1000%. It is important to note that chemical vapor smoothing redistributes the surface material to provide a sealed, smooth surface but does not produce a polished surface. There will still be visible surface topology and minimal layer lines.
Chemical vapor smoothing can significantly improve the viability of 3D printing in food processing, medical devices, and consumer products and is recommended for end-use applications in these industries.
Other benefits of chemical vapor smoothing include
- A uniform, sealed surface, on 3D printed parts
- Improved tensile, elongation, and flexural performance
- No extra coatings; the surface is the part's material
- Significantly reduced moisture absorption
- Closed loop, repeatable processing results
- Ability to polish non-line-of-sight features
- Retains features and dimensional accuracy
- No residual chemicals or media in features
- Improved cosmetics and enhanced colors
Design Tips for Vapor Smoothing 3D Prints
- Add radii to sharp internal corners to prevent rounded voids
- Keep wall and feature thicknesses above 0.040" (1 mm) to avoid distortion or defects
- Keep wall thicknesses uniform, similar to injection molding
- Be mindful that orientation-specific build lines may still be present, but smoothed
- Racking marks may be visible depending on how the work was held during processing
- Flexible materials, like TPU 88A, may have more surface imperfections versus rigid materials
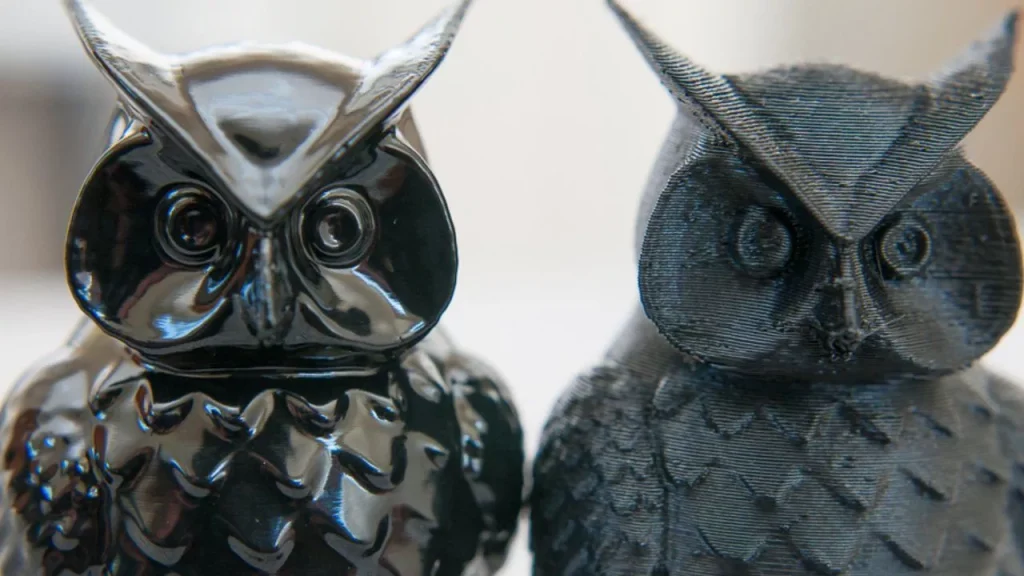
Applications for Vapor-Smoothed Parts
Vapor smoothing on printed medical parts enables aesthetic designs that are comfortable, easy to clean, and sweatproof. It’s also ideal for automotive and industrial machinery as it produces smooth, tactile, leak-proof 3D-printed parts. These properties allow for a wide range of applications, from concept modeling to prototyping testing and end-use parts.
Typical use cases include:
- custom medical devices
- wearables
- liquid reservoirs and tanks
- fluid transfer pipes and manifolds
- ducts
- valve covers
- oil sumps
Ready to bring your production to the next level?
If you’re interested in trying our Vapor Smoothing process, write in to us and get a free consultation for your 3D prints.