Selective Laser Sintering (SLS) 3D Printing Service
Elimold has printed over 1 million parts and has mastered the process of manufacturing parts using our in-house library of SLS machines. We specialize in delivering the highest quality plastic parts tailored to your individual needs. Simply design the CAD drawing of the part you want and send it to us, and we’ll do the rest. Of course, our experts will review your design and help you manufacture an even better part. Contact us today.
Professional SLS 3D Printing Service Provider
Experience Elimold’s SLS 3D printing expertise now and build the future of manufacturing. Choose us, choose innovation, precision and unparalleled quality. We pride ourselves on pushing the limits of SLS technology. Our team of experts uses advanced equipment to create precise, high-performance parts through SLS nylon 3D printing technology. Whether you need a prototype, a functional part or a complex design, we can deliver results that exceed expectations. Trust Elimold to meet your SLS 3D printing needs and open up endless possibilities for your project.
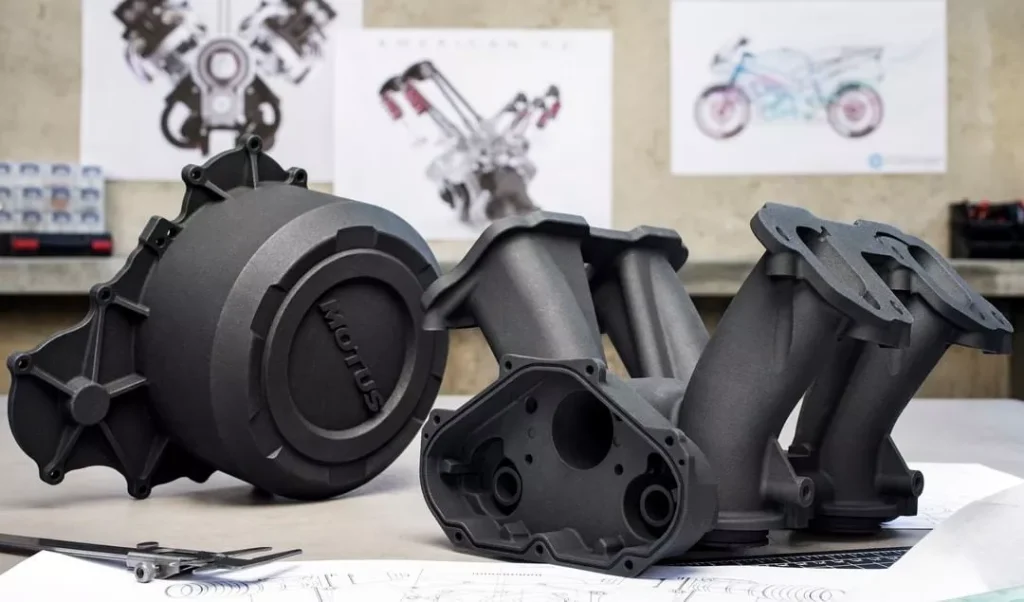
Looking for an industrial SLS 3D printing service?
Are you looking for an industrial SLS 3D printing service to build strong and durable parts with complex organic geometries? Whether you are a designer or an engineer, Selective Laser Sintering (SLS) technology gives you the freedom to create complex, high-quality parts with unparalleled precision. SLS is a proven industrial 3D printing process that engineers trust. It is a flexible tool that produces affordable, high-fidelity plastic parts for both prototyping and mass production. SLS prints parts with finer details than most additive manufacturing processes using high-strength plastics. This makes it ideal for applications that require heat and impact resistance. Elimold can provide machines in a variety of sizes and capacities to meet all your SLS production needs.
Experienced SLS 3D Printing Manufacturer
At Elimold, we are not only leaders in SLS 3D printing, but also pioneers, setting new standards in precision and quality. With years of SLS experience, our commitment to innovation and excellence makes us the partner of choice for industry leaders seeking the highest precision and reliability. Our in-house state-of-the-art factory in Shenzhen, China, with large-format SLS printing equipment, enables us to additively manufacture SLS parts with unparalleled capacity, precision and finish, and we focus on demanding SLS projects for the production of end-use parts. And we can provide a rich selection of nylon materials, combined with professional finishing services, to customize each project to exceed the highest expectations of our customers. And we are tirelessly committed to improving our material and process validation, consistency and compliance. Because at Elimold, we don’t just meet the standard, we define it.
SLS 3D Printing Factory
Elimold has a proven track record of manufacturing high-quality, high-precision SLS 3D printed parts for customers around the world. With our expertise and in-house 3D printing factory with over 120 of the latest SLS 3D printers, our engineers’ attention to detail and our entire team’s commitment to quality excellence at every stage, you can be assured that by choosing Elimold, you will receive the highest quality SLS 3D printed parts. This is also the basis for ensuring our competitive pricing and unlimited production capacity. Internally, we use data to track on-time delivery, quality and price, which ensures that your work and SLS 3D printed parts are always provided by the most appropriate supplier.
Our SLS Production Capabilities
Elimold wants every innovator to make an informed decision. We are working hard to make all information as transparent as possible. Here are some technical data of our production capabilities for your reference.
- Maximum build dimensions: Dimensions are unlimited as components may be composed of several sub-parts. The maximum build envelope is 630 x 330 x 550 mm
- Standard accuracy: ±0.3% (with a lower limit on ±0.3 mm)
- Layer thickness: 0.12 mm
- Minimum wall thickness: 1 mm, but living hinges are possible at 0.3 mm
- Surface structure: Unfinished parts typically have a grainy surface but various post-production finishes are possible
- Lead time: 2-3 days
Our Equipment Capabilities
SLS industrial 3D printers have build volumes that vary in size; our small printers have a build volume of 200mm x 250mm x 330mm, and our EOS printers have build volumes ranging from 650mm x 350mm x 550mm to 700mm x 380mm x 580mm, with layer thicknesses of 100 to 120 microns. Thousands of parts can be included in a single build, with greater precision and repeatability than most technologies.
Free DFM Analysis Report
Elimold’s experienced team of engineers has deep engineering expertise in various digital manufacturing methods. Before manufacturing your product, our engineers usually consider the capabilities of the final manufacturing process and provide you with a Design for Manufacturing (DFM) analysis report. Our SLS 3D printer can print complex geometries that are impossible or cost-prohibitive to manufacture with traditional manufacturing methods. It also allows designers to combine complex components that are usually made by multiple parts and different processes into one part. Therefore, we can not only help you optimize part design for Selective Laser Sintering (SLS), but also help you achieve high-volume production using injection molding and other production methods.
SLS 3D Printing Rapid Prototyping Services
Our high-quality SLS prototyping services accelerate your product development. Using Selective Laser Sintering (SLS) technology, we deliver durable and precise prototypes that are ideal for functional testing, fit checking, and end-use applications. Whether you need a single part or small batch production, our SLS process ensures superior mechanical strength and detail accuracy without the need for support structures. Engineers, designers, and startups trust our SLS prototyping services, which are ideal for complex geometries and industrial-grade components. With extensive experience in customer-centric SLS 3D printing, we are ready to work with you to gain a deeper understanding of your project and find solutions to ensure maximum success in every aspect of your production process. We support these goals with a selection of materials, custom processing and value-added services, high-quality machines, and excellent customer service.
Fast Turnaround for SLS Custom Parts
We are unique in our commitment to fast delivery of production-ready parts. We know time is of the essence, which is why we offer a streamlined production process that allows us to efficiently move from design to finished product. All parts are available in as little as 5 days, so you get your parts fast without compromising quality. And we pride ourselves on fast delivery speeds, ensuring you can meet project deadlines seamlessly. Our streamlined processes and advanced technology ensure that all of your SLS 3D printing needs are hassle-free. Choose Elimold for SLS 3D printing services and receive exceptional results, unmatched quality, and a trusted partner for your business.
Turn your ideas into reality with our advanced services
Please feel free to contact our technical experts. Our design team and consultants will evaluate your project. We will provide you with solutions and free consultation.
On-Demand SLS 3D Printing Services
We offer on-demand additive manufacturing and SLS 3D printing services. From rapid prototyping to appearance models and mass production, Elimold’s dedicated team has the latest technology and expertise to handle any additive manufacturing project to bring you the best results, and advanced 3D printer equipment ensures excellent print quality and reliability. We understand the complexity of the process and can guide you through every step of the manufacturing process. You can choose from a variety of polymer materials and surface treatments, and then let us produce them in our ISO 9001 certified facility. In addition, we take a personalized approach to each project and tailor our services to your unique needs to ensure your success. Whether you need a one-off prototype or large-scale production, we can help you.
Quality Management Standards
We recognize that quality is critical to the success of any manufacturing project, and we are committed to providing the best quality assurance in the industry. From the initial SLS 3D printing service quote to final inspection, our experienced engineers will triple-check all of your files and parts to ensure you are satisfied with your print results every time. With our EN 9100:2018, ISO 9001 and ISO 13485:2016 certifications, you can trust us to provide reliable, high-quality products that meet the most stringent industry standards. In addition, we are able to generate initial sample test reports and measurement reports in our in-house measurement laboratory, and with the GOM ATOS Capsule 3D scanner, we can create target vs. actual color comparisons to identify potential color deviations. So at Elimold, we produce your custom parts to strict manufacturing standards and ensure that all parts and processes comply with industry standards. The inspection report we provide with each order contains a comprehensive verification of these requirements.
How do we provide SLS printing services?
We are committed to managing SLS Selective Laser Sintering projects in a unique way and in close collaboration with our customers. Our expert engineers and other professionals work with customers from the beginning to understand their goals and discuss every step from prototype to production when necessary. Our project engineers will guide you in choosing the most suitable material for your prototype to ensure the best results. However, we never compromise on quality standards when designing a prototype in the ideal shape. Our team will discuss project delivery requirements, timelines, and costs. Our goal is to maintain transparency in the selective laser sintering printing process. In most cases, we use chemically resistant thermoplastics to create prototypes. You will find that it is precisely because of the use of this material that the product is extremely durable.
Selective Laser Sintering (SLS) Material Options
- PA 11 Black(PA 850)
- PA12 Black
- PA 12 White (PA 650)
- PA 12 Value
- PA12 Mineral-Filled (PA620-MF)
- PA12 40% Glass-Filled (PA614-GS)
- Polypropylene Natural
- TPU 70-A
Finishing Options for SLS Parts
Straight from the build table, SLS parts have a rough, porous finish. A variety of finishing options are available to enhance their appearance and performance, including:
- Sanded
- Tumbled
- Media blasted
- Vibratory Tumbling
- Dyeing
- Painting
- Ceramic Coating
- Powder Coating
- Liquid Polymer
- Polishing
- Dyed
- Plated
- Decals
- Pad printed
- Screen printed
- Inserts
- Post machined
- Assembly
- Painted (customer spec paint)
- Specialty coating
Vapor Smooth SLS 3D Printed Parts
Elimold can vapor smooth 3D printed parts to achieve a superior surface finish. Vapor smoothing is a batch automated smoothing process that produces a high-quality surface. Combined with the low-cost SLS technology, this surface finish can make parts comparable to injection molding in form and function. Vapor smoothing creates a uniform, sealed surface with a semi-gloss appearance. SLS parts can be dyed. The enhanced surface also improves the overall performance of the 3D printed part, including ultimate tensile strength, flexural yield strength, and elongation at break. Vapor smoothing can be applied to HP Multi Jet Fusion, Selective Laser Sintering, and Fused Deposition Modeling parts, and is suitable for both hard plastics and elastomers.
Applications of SLS 3D Printing
SLS uses production-grade nylon materials to create parts that are as strong, functional, and durable as those made using traditional manufacturing techniques. The durability of SLS makes it an ideal technology for the following applications:
Rapid Prototypes
- Prototypes with functioning proofs of concepts
- Models for Design Evaluation (Form, Fit & Function)
- Product Testing & Performance
- Verification of Engineering Designs
- Models for Wind-Tunnel Tests
Tooling and Patterns
- Quick Tooling (concept development & bridge tools)
- Visual Aid for Tooling and Manufacturing Estimating
- Patterns for investment casting
- Jigs and Equipment
- Sand casting foundry patterns
Ready to Get Started?
From design to prototype and production, our team of engineers is ready to help bring your idea to life with SLS 3D printing.
SLS 3D Printing Parts Supplier
Elimold has a professional team of engineers and production capabilities to provide more diversified, efficient and cost-effective SLS 3D printing solutions for different application scenarios of industrial customers. Moreover, SLS is the first choice for producing parts with tight tolerances and complex designs, making it one of the most widely used and popular additive manufacturing technologies today. We are always committed to the highest quality standards of SLS 3D printing to ensure that each part always meets your specifications. Our powerful system closely monitors every aspect of material handling, recycling, equipment maintenance and process control to ensure material traceability, mechanical property verification and dimensional accuracy. From functional prototypes to end-use parts, our rich SLS experience provides unparalleled precision and accuracy, making Elimold the preferred supplier of SLS 3D printing services.
How does SLS 3D printing work?
Selective Laser Sintering (SLS) is an industrial 3D printing process that produces accurate prototypes and functional production parts in as little as 1 day. A wide range of nylon-based materials are available, which can produce highly durable final parts. The laser selectively melts a thin layer of plastic powder. The part is built layer by layer in a powder bed. The laser sintering machine applies a layer of plastic powder to the build platform and then melts the powder with a laser (or multiple lasers). The build platform is then lowered and the next layer of plastic powder is laid on top of it. By repeating the process of laying down powder and melting where needed, the part is built in the powder bed. Once the build is complete, the entire powder bed, along with the encapsulated part, is moved to a disassembly station where it is lifted and the part is removed from the powder bed. First, it is manually brushed to remove most of the loose powder. The part is then sandblasted to remove any remaining powder and sent to the finishing department.
Can SLS 3D Printing Create Metal Parts?
Standard SLS printing is not designed for metal. However, metal 3D printing processes such as DMLS (direct metal laser sintering) and SLM (selective laser melting) are based on similar principles. They use a similar powder bed fusion method, but operate at higher temperatures and use different types of lasers. So, while SLS printers cannot print metals natively, the powder bed fusion technology family definitely includes systems that are compatible with metals.
Advantages of SLS 3D Printing
- Functional Parts & Prototypes
- No Support Material Needed
- Fast Process
- Parts With Complex Geometries
- Good For Small To Medium Batches
- Good Isotropic Mechanical Properties
- Great For Layer Adhesion
- Reuse Unused Material
- Dye Different Colors
SLS Design & Build Guidelines
Each 3D printing technology is a little different, here are standard guidelines to consider when choosing SLS as your 3D printing process:
- Build Layers: 0.004”
- Minimum Wall Thickness & Feature Size: 0.030”
- Standard Finish: Level 2 Bead Blast
- Finish (see more available custom finishes)
- Standard Lead Time: 3-5 days
- Tolerances: +/- 0.005” for first inch then +/- 0.002” per inch thereafter
- Inserts: Install in post-processing with adhesives
- Holes: Drill, ream and tap
Ready to get started on your Selective Laser Sintering (SLS) 3D Printing quote?
Create components with tough mechanical properties & complex geometries.
Online Selective Laser Sintering 3D Printing Service
We provide high-quality online Selective Laser Sintering 3D Printing services. Selective Laser Sintering (SLS) is one of the most popular 3D printing technologies, capable of producing high-precision and durable parts, ideal for end-user, small and medium-volume production or rapid prototyping. A wide selection of printing materials and fast delivery times are our strengths. In addition, SLS is an ideal technology for many rapid prototyping or rapid tooling applications. Since SLS has a much higher throughput and speed than some other additive manufacturing technologies, it can quickly prototype and test new customized parts or components. The advantage of SLS is that it can print high-durability final parts that require heat resistance, chemical resistance, flexibility or dimensional stability. In addition, SLS 3D printing does not require support structures, so multiple parts can be easily nested in one model, and since there is no need to remove support structures, there is less risk of damage to the complex internal geometries that 3D manufacturing can produce.
Industries We Serve
Designers and engineers across numerous industries have used SLS printing in their product development process. While SLS can be used for prototyping, it is also for functional, testing, and production parts. Applications of SLS include:
- Consumer Goods
- Sports
- Aerospace
- Automotive
- Product design
- Architecture
- Industrial machinery
- Robotics
- Medical and Dental
- Footwear
- Consumer electronics
- Drones
Common SLS 3D printed parts
SLS 3D printing and the SLS manufacturing process are extremely versatile and are used in a wide range of industries and applications. From rapid prototyping to produce test parts in a few days, to engineering-grade parts suitable for production environments. Whatever the application, our 3D printed parts accelerate time to market, inspire innovation, reduce prototyping costs, and provide unparalleled precision. The following are common SLS parts:
- Gears
- Housings
- Brackets
- Enclosures
- Ducts
- Clips
- Hinges
- Mounts
- Casings
- Spacers
- Connectors
- Adapters
- Prototypes
- Functional models
- Grips
- Fixtures
- Jigs
- Handles
- Structural supports
- End-use parts
- Medical devices
- Orthopedic models
- Surgical guides
- Automotive components
- Interior panels
- Custom tools
- Snap-fit assemblies
- Drone parts
- Robotic components
- Bike parts
- Aerospace ducts
- Custom fasteners
- Cooling channels
- Packaging inserts
- Architectural models
- Consumer electronics shells
- Footwear midsoles
- Helmet liners
- Sensor housings
- Battery holders
Other 3D Printing Services
We offer a wide range of cutting-edge 3D printing services, and with the power of Elimold, you can turn your unique ideas into viable, high-performance solutions. Whether you want to enhance your product line or create a custom solution, our 3D printing services provide you with the flexibility and quality assurance you need. Partner with us to explore the endless possibilities of our many 3D printing services across a variety of industries and applications.
Stereolithography (SLA)
PolyJet
Multi Jet Fusion (MJF)
Digital Light synthesis(DLS)
Fused Deposition Modeling (FDM)
Direct metal laser sintering (DMLS)
P3 technology (DLP)
Solidscape (wax deposition)
Micro 3D Printing
Wire Arc Additive Manufacturing (WAAM)
Metal Binder Jetting
Selective Laser Melting (SLM)
Ceramic 3D printing
Metal 3D Printing
Differences between SLA and SLS 3D Printing
While both SLA and SLS are considered high-precision 3D printing technologies, they differ significantly in terms of materials, applications, and operational requirements. SLA (stereolithography) uses a light source to solidify liquid resin into smooth, detailed parts, ideal for visual prototypes, dental models, and complex designs. SLS (selective laser sintering) uses powdered thermoplastics to produce strong, durable, mechanically excellent, functional parts without the need for support structures. SLA is best suited for aesthetic, small-scale applications, while SLS excels in industrial-grade, performance-driven use cases where strength and durability are critical.
The Difference Between SLS 3D Printing and SLM 3D Printing
Selective Laser Melting (SLM), sometimes referred to as Direct Metal Laser Melting (DMLM), uses a laser to melt metallic powders in successive layers. The machine fully melts the powder before another bed of powder is added above the melted layer. SLM causes the metal granules to melt together to fully form one homogeneous piece. The primary difference between SLA and SLS is the material used for each process. SLS can be applied to plastics, glass and ceramics, whereas SLM is used exclusively for metal alloys.
Differences between SLS 3D printing and FDM 3D printing
FDM extruders extrude heated filament through a nozzle. The extruder is mounted on a gantry system, so it is very similar to a hot glue gun. The movement rate and speed of the nozzle is limited by the extrusion rate of the heated filament. SLS is not limited by this because the material is not extruded, but melted by a laser moving along a raster path at speeds of up to 5000 meters per second. This makes SLS an extremely fast and precise 3D printing method. With SLS printing, production time can be greatly reduced due to the high speed of the laser. It takes about 20 parts before the production time doubles. Generally, SLS printing speeds are 8 times faster than FDM printers on average, and even 20 times faster in some cases. SLS is a high-throughput, high-productivity form of 3D printing.
SLS 3D Printing vs. Plastic Injection Molding
SLS 3D printing excels when you need durable plastic parts. SLS parts are known for their toughness and durability, and their performance is comparable to parts produced by traditional manufacturing methods such as injection molding. In addition, when plastic parts need to be produced in small batches, we often encounter the question of which manufacturing process is the most cost-effective. If you are not sure whether SLS 3D printing or plastic injection molding is the best process for your component or assembly, we are happy to provide you with a comparative quote. If you need plastic parts made of injection molded materials or need a large number of parts, we recommend the rapid processing process of injection molding for the production of prototypes and small batches. When plastic parts need to be produced in large quantities, plastic injection molding is more cost-effective than SLS 3D printing.
One-Stop SLS 3D Printing Manufacturing Service
Selective Laser Sintering technology is not just for prototyping. It can also be used to produce low-volume production parts, which is ideal if you are waiting for injection molds to be manufactured. SLS works with thermoplastics. This means it can be used to quickly create functional prototypes of new product designs. Once the part design is complete, you can move to injection molding for production. With our cross-functional engineering expertise, we can help you adapt your part design to work well in both production environments. SLS can be used to build workholding devices to hold metal parts for CNC machining. Because SLS can achieve a large build volume, precision of small features, and high mechanical strength, it is ideal for large jigs and fixtures. If tight tolerances are required, 3D printing technology can be used to add additional material to critical surfaces. Then, it can be machined to the required tolerances.
Request Your Free Selective Laser Sintering (SLS) 3D Printing Quote Today
After receiving your drawings, our engineers will analyze your custom Selective Laser Sintering (SLS) 3D Printing parts right away. We actively work with you to clarify all details before providing a quote that is both economical and accurate.