Liquid Silicone Rubber (LSR) Injection Molding Services
Manufacture custom liquid silicone rubber prototypes and end-use production parts in 15 days or less using a wide range of durometers and grades of LSR materials. Our state-of-the-art facilities feature lights-out capabilities, fully automated Liquid Injection Molding (LIM) cells, in-line vision technology, value-added operator stations, and finely tuned quality systems, all of which ensure we deliver high-quality, high-volume LSR parts to our customers. Contact us now for a free instant quote.
Professional Liquid Silicone Rubber Injection Molding Manufacturer
Whether you are looking for a single Liquid Silicone Rubber (LSR) component design or a complete device with LSR components, Elimold can help. From design for manufacturability to mold design, to liquid injection molding and assembly. Our team of experts has decades of experience designing and molding components with materials that have a wide temperature range (-94°F to +400°F), low compression set, and resistance to sunlight and ozone depletion. Elimold’s proven LSR process is trustworthy and can ensure that your parts meet specifications, quality, and are delivered on time. If you are looking for a professional LSR parts manufacturer, choose Elimold. We are committed to providing high-quality LSR injection molding solutions with precision and efficiency.
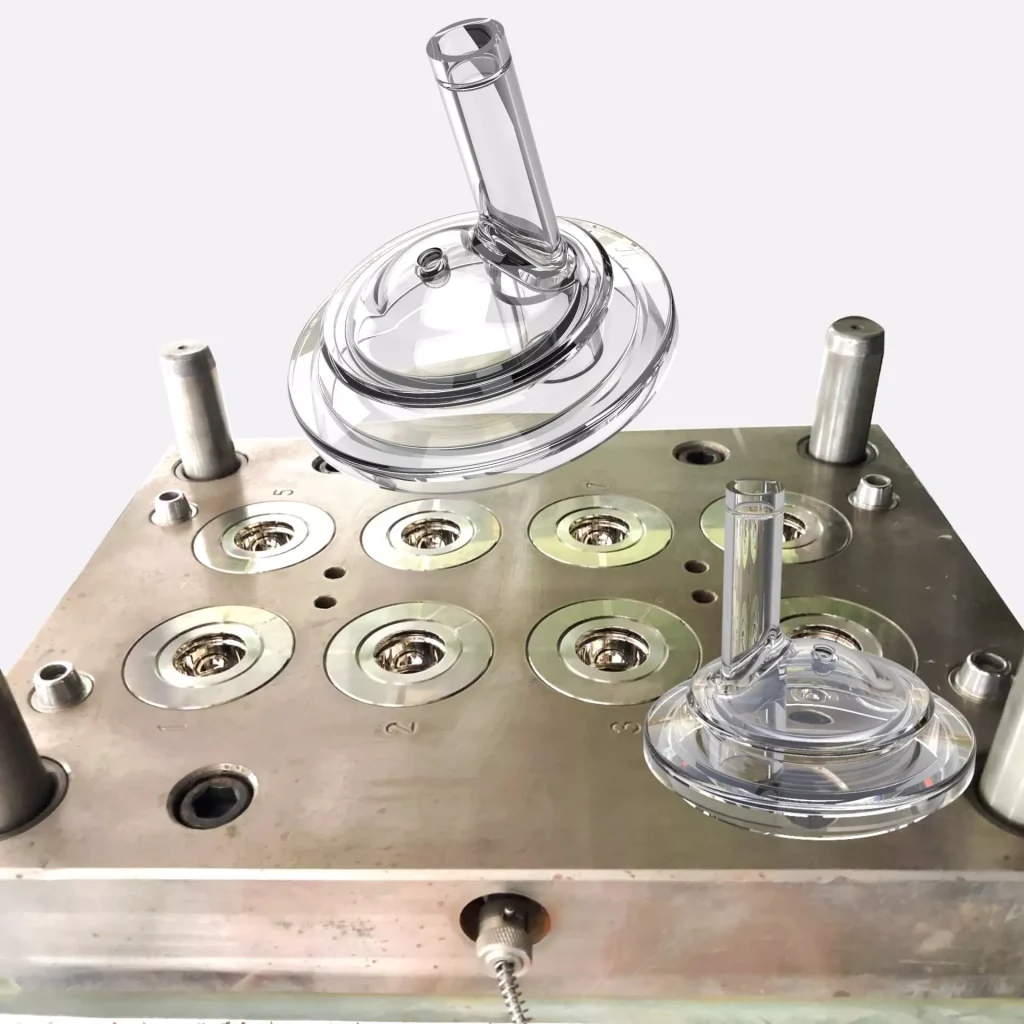
End-to-End Liquid Silicone Injection Molding Services
Elimold offers end-to-end liquid silicone injection molding services, specializing in rapid prototyping with production-grade liquid silicone rubber. Our expertise includes material selection support and automated design for manufacturing (DFM) analysis to help ensure efficient, high-quality production. We are able to undertake projects from initial prototyping to full production and support the complete product lifecycle, with capabilities including 3D printing, polyurethane casting, traditional and specialty injection molding technologies such as overmolding, gas-assist molding, and in-mold decoration, as well as assembly, testing, and packaging.
At Elimold, we help you make informed decisions about the manufacturing method that is best for your product. When evaluating LSR, it is important to consider your material needs, design complexity, regulatory compliance needs, and production volume and speed. Our experts will guide you every step of the way.
Liquid Silicone Rubber Injection Molding Factory
We have an in-house advanced liquid silicone parts manufacturing factory. The factory covers an area of 25,000 square meters, has 300 employees, 70 LSR injection molding machines, 70 sets of feeding systems, 36 VOC purification furnaces, 30 measuring instruments, and all molding and production workshops are 100,000-class clean rooms. After long-term development and improvement, we have established a strict and complete quality management system, tested and evaluated product quality at each production link, and passed all SOPs and certifications such as ISO9001, ISO14001, ISO45001, ISO13485, etc., and can provide you with cost-effective LSR injection molding products. Compared with other silicone molding manufacturers, Elimold’s production team is more experienced and more dynamic. Our team of engineers has complete and professional knowledge and experience of a full range of silicones covering various characteristics and performances. In addition, we always regard custom LSR injection molding production as the top priority of our business, focusing on providing customers with the most suitable solutions and reliable products.
Cleanroom Liquid Silicone Rubber Molding Shop
Innovation is key to providing cutting-edge solutions to improve the manufacturing of liquid silicone rubber parts. In addition to cutting-edge LSR molding capabilities, Elimold also has a 30,000 square foot Class 8 cleanroom. This sterile environment provides optimal conditions for the molding and assembly of silicone products, ensuring the highest level of cleanliness and product integrity. The Class 8 cleanroom ensures that the LSR molding process is completed in a controlled and contamination-free environment. This is essential for the production of medical-grade components, where precision and cleanliness are of paramount importance. In addition, our expertise is not limited to molding, and we also provide a comprehensive range of secondary processing, including assembly services. This means that medical companies can rely on Elimold to handle a variety of post-molding tasks, such as advanced and complex electromechanical assembly, cleanroom assembly, and sterilization management. This simplifies the manufacturing process and reduces time to market.
Custom LSR Parts Production
We can offer a wide range of options for LSR parts production. We carefully evaluate each project to determine the best LSR injection molding technology and offer a variety of LSR parts production options. We carefully evaluate each project to determine the LSR injection molding technology that is best suited to produce the part: LSR, LSR two-color injection molding, LSR multi-color injection molding or LSR overmolding. Our state-of-the-art facilities are equipped with climate control and extremely high cleanliness. Our production areas are clean and dust-free, and the LSR, LSR 2K, multi-color injection molding and overmolding production cells are fully automated to minimize human contact. Many liquid silicone products have strict cleanliness requirements and require specific ISO-certified hygienic production standards. To meet these requirements, Elimold is equipped with single-line and secondary LSR production lines.
In-House Liquid Silicone Rubber Injection Mold Manufacturing Services
Before we can produce your silicone parts, we first make the mold. Once you place your order, our mold engineers begin designing the ideal mold for your part. Once the design is complete, the mold goes to our mold manufacturing department. All Elimold silicone molds are made from high-quality steel and aluminum, using CNC machining and EDM to create the mold cavity. Once the mold is completed, we begin testing the mold and measuring all dimensions to ensure it meets your specifications.
Our in-house mold manufacturing will completely change your project’s speed to market. Imagine seamless communication between your team of designers and mold manufacturing engineers, which speeds up development and brings your products to market faster. Straightforward quality control ensures that the mold meets your exact specifications and reduces defects. In-house mold manufacturing keeps everything streamlined, which can potentially save costs. This is a strategic advantage for any serious injection molding company.
Ready to Get an LSR Injection Molding Quote?
Get custom liquid silicone rubber parts in as little as 15 days. We use aluminum or steel tooling, offer cost-effective processing options and faster production cycles, and stock a wide range of LSR grades and durometers.
Custom LSR Solutions for Your Business
Elimold specializes in liquid silicone rubber parts manufacturing and has mastered the production of high-quality LSR parts and LSR two-shot and multi-shot parts. Our expertise in this field allows us to customize the entire process to your specifications for true innovation. We offer Extraordinary LSR Solutions™, taking “customization” to a new level. Since its inception, Elimold has been a leading manufacturer of liquid silicone rubber parts, serving some of the largest companies in the world. Our advanced capabilities cover all aspects of the design and production process. We can help you select the right LSR grade for your part, provide part design support to optimize manufacturability (DFM) and part performance, provide premium, 101-grade tooling and high-volume part production, and in-line value-added solutions to keep your overhead costs low and provide high value.
Integrated Solutions for Liquid Injection Molding
Our experienced team of engineers provides the most appropriate solutions based on the specific needs of each project. From product design, mold manufacturing, material selection, production process to final delivery, we participate in and optimize every link to ensure the most cost-effective production solution. Our in-house factory is equipped with industry-leading high-precision equipment to meet complex process requirements. Our production environment follows strict hygiene standards, and large-scale production is carried out in ISO Class 8 clean rooms to ensure high quality and consistency of products. Therefore, all LSR products produced by Elimold are safe and reliable and produced in a dedicated, clean environment. We often supply companies with the most stringent cleanliness requirements in the industry. Our parts are often used in the medical field, where the cleanliness and safety of the parts are of paramount importance. Therefore, we have set up a dedicated production area for all LSR products and are committed to producing products that are as clean and safe as possible. In this way, we have all LSR technologies in one place, thereby passing on cost savings to our customers.
Liquid Silicone Rubber Injection Molding Turnkey Solutions
Our team of experts has decades of knowledge and experience in LSR injection molding. We provide a full range of services, from early design and prototype support to custom manufacturing processes and quality systems, to create greater value for our partners. We also provide custom solutions to meet the specific needs of each project and provide high-precision, high-volume, high-quality liquid silicone rubber injection molded parts.
Design & Prototype Services
Mold Tool Design and Fabrication
Rigorous Material Selection
CNC Machining
Medical Molding Methods in Cleanrooms
Secondary Operations
LSR Injection Mold Making Shop
If you need a custom LSR mold making solution, Elimold Mold Making Shop is ready to help. We use durable materials such as steel or aluminum to create precision plastic molding tools to produce quality products. We use injection molding equipment to create standard designs based on customer needs. Our team has more than 20 years of experience in LSR injection mold making and operates high-quality equipment. The mold making shop covers an area of 2,200 square meters to streamline the production process. The mold processing process is simplified through streamlined solutions. We provide single-cavity and multi-cavity design options as well as manufacturability analysis and mold flow analysis, and also provide quality documentation.
In addition, all new LSR injection molds we manufacture are tried and verified to ensure that all part dimensions are correct and the mold functions properly. We use scientific injection molding technology to establish consistent and repeatable LSR injection molding process parameters to control the molding process and ensure the production of consistent quality parts at a lower total cost. Elimold focuses on part design, mold design, thermoplastic material selection, and measurement of plastic injection molding process parameters to systematically eliminate variables that could lead to defective or poor quality parts.
One-stop LSR Mold Making Service
Elimold’s LSR injection mold making is based on the concept of teamwork. From the very beginning, we actively involve our customers in the development process and develop custom solutions. The success of the project depends on the close cooperation between our experienced team and our customers. Therefore, we maintain open and transparent communication. From the initial development stage, we work together to take all aspects into consideration. In the end, we create innovative, efficient and high-quality molds. Our commitment does not end with the completion of the mold. We accompany our customers throughout the service life of the mold and provide advice at any time. This long-term support is an important part of our service. At Elimold, we rely on partnership and teamwork to develop the best solutions with our customers and ensure sustainable cooperation.
LSR Tooling and Molding
Perfect precision LSR parts begin with tooling. Tooling requires a combination of CNC machining and EDM (Electrical Discharge Machining) techniques. Manufacturing LSR tooling that can withstand the high temperatures of the LSR molding process requires time and extreme precision. LSR tooling can be the most time-consuming and capital-intensive part of the silicone rubber molding process. However, LSR’s ability to flow into very thin cross-sections, small radii, and thick/thin features makes tooling design much simpler. In addition, the mold surface does not need to be highly polished, nor does it require draft angles to aid in demolding the finished part. Once the solidification phase is complete, the molded part can be ejected from the mold without fear of deformation or damage.
LSR Cold Runner Mold Solution
With professional services and unremitting efforts, we are committed to meeting the quality requirements of all kinds of customers. We have an experienced R&D team, and the core technical team focuses on product design, mold design, mold manufacturing and liquid silicone rubber injection molding. The self-developed LSR cold runner system is our core technical value, and the adaptive cold runner system can flexibly adapt to single-cavity or multi-cavity LSR cold runner systems for different products. Elimold has successfully developed many business cases in the past few years. We provide customers with value-added custom solutions and comprehensive support from concept to mass production. We have advanced fully automatic LSR injection molding technology, ISO-certified Class 8 clean rooms, strict quality systems, and end-to-end project management to ensure that we can provide consistent high-quality parts, meet your precise specifications, and optimize your product performance.
Common Tolerances for LSR Parts
Tolerances for standard applications typically range from ±0.1 mm to ±0.2 mm. Many factors affect these tolerances, including part geometry, the accuracy of the mold used, material shrinkage during curing, cavity balance, and proper venting. These variables must be carefully managed to ensure the desired accuracy and consistency of the final part. Elimold’s proven liquid silicone rubber process technology, with speed and capacity, can help you meet tight deadlines. With decades of experience, our vertical integration ensures that you get the exact parts you need.
Liquid Silicone Rubber Injection Molding Capabilities
Different parts require different production methods depending on their materials and applications, but every part requires high-quality production standards and fast delivery times. As one of the top choices for custom liquid silicone rubber parts manufacturers, Elimold is able to quickly and accurately manufacture parts using a variety of production methods listed below. Contact us today to provide your product specifications and get a quote, and learn how we can help you complete your project.
Liquid Silicone and Rubber Overmolding
Silicone Micromolding
LSR Compression Molding
Silicone Prototypes
Silicone Insert Molding
Silicone Extrusion
LSR Rapid Prototyping Services
The process begins with early involvement at the front end of the project. Elimold engineers work closely with customers to gain a deep understanding of the function and goals of the component. With years of experience and a comprehensive understanding of LSR materials and injection molding, our team is able to provide customers with design support to achieve optimal manufacturability and part performance.
Prototypes are often necessary and are used for a variety of purposes. We have a variety of rapid prototyping methods to choose from, depending on time, cost and quality requirements. Elimold often uses 3D printing services for early stages when a small number of parts are required. If a small number of parts are required in a short period of time, LSR parts can be produced using vacuum casting, which provides better appearance and function. Elimold can provide customers with the best support when production-quality injection molded LSR parts are needed for final testing, pilot production or production tooling.
From Prototype to Series Production
We have produced and delivered up to 10,000 custom LSR parts in a week and offer the fastest LSR production tools on the market. High and low volume production needs are no problem for our experienced team of professionals. We can design custom LSR products to your specifications in the fastest way possible. No matter what industry you are in, our experienced team of professionals can meet your specific needs. And our state-of-the-art in-house facilities guarantee your projects and parts are delivered to you 24/7/365. Therefore, we understand what it feels like to be under great pressure to meet deadlines. Our primary goal is to make it easier for you to meet deadlines. If you would like a quote for a specific project, please contact us. We look forward to serving all of your projects, no matter how big or small.
Design for Manufacturing
Design for Manufacturability (DFM) is your secret weapon for transforming innovative concepts into production-ready LSR injection molded parts. By working with our DFM experts early on, you can identify potential roadblocks, such as complex geometries or uneven wall thicknesses. We’ll recommend adjustments to optimize your design for efficient molding, minimizing waste and production costs. This ensures that your parts are not only fully functional, but also easy to manufacture, saving you time and money while turning your vision into reality.
Designing and Creating LSR Prototypes with Manufacturing in Mind
Some customers call us after discovering that the prototype they contracted to build had a minor flaw when it was delivered: unfortunately, this prototype can’t go into production. You might be surprised how often this happens; in the rush to build a prototype quickly, designers and engineers with little elastomer experience end up with a design that looks perfect, but can’t be manufactured at scale. We work with you early in the project to focus on quality and better understand the design input and output requirements of your custom part. Having a better understanding of the design intent of your product will help to launch the product more smoothly and greatly reduce future risks. We will help you answer questions such as:
- Do you need an early-stage prototype or a manufacturing-quality replicate prototype?
- How many cavities will be needed in the tool to support the volumes needed for development?
- Where are your critical sealing surfaces and functional areas?
- Where can we place gates and parting lines?
- What are the general operating conditions as to temperature, fluid contact, cycles rates?
Reverse Engineering Service
Our unique full-service production model covers the entire process from silicone molding to assembly, packaging and delivery, saving customers time, cost and warehouse space. This streamlined process provides efficient production solutions. More importantly, our team of engineers have many years of experience in the production of liquid silicone rubber molding products. Even if you don’t have technical drawings, we can directly reverse engineer based on samples to provide you with custom liquid silicone rubber parts from simple to highly complex. If you want to manufacture reliable and innovative silicone products, Elimold is your best choice. Our commitment to quality and customer satisfaction makes us a trusted industry partner.
LSR Quality Management and Standards
Whether it’s product design, mold making, prototyping or new product manufacturing, your silicone rubber molding manufacturer must have the ability to meet the most demanding specifications and an unwavering commitment to delivering the quality you expect. The most stringent quality assurance standards for liquid silicone rubber injection molding should include a variety of elements. LSR parts manufactured at Elimold are constantly monitored for defects, damage or any other inconsistencies. Our quality inspection team uses data control numbers to assign and record the call number of the material batch for each part manufactured, which can trace each product back to the date of manufacture, the manufacturing process performed and the materials used. Elimold’s quality management program ensures that parts are produced right the first time, saving you time, cost and maintaining your reputation.
Quality Inspections
Depending on your application’s requirements, you can choose from the following when requesting a quote for your silicone rubber products.
- Quality Inspections available for on-demand manufacturing orders
- Designing for Manufacturability (DFM) Feedback
- Scientific Molding Process Development Report
- In-process CMM inspection and machine monitoring
Quality Inspection Technology
Elimold has professional inspection technology for liquid silicone rubber injection molded parts. We use special technology to inspect soft and flexible materials such as liquid silicone rubber (LSR) to ensure the quality and performance of the parts. Visual inspection is often used to detect surface defects such as flash, voids, insufficient injection, flow marks and discoloration to quickly evaluate the external condition of the part. For more accurate measurement, we use non-contact methods such as laser scanners, vision systems or optical comparators to evaluate the dimensions of the part. In some cases, we use custom fixtures or 3D printed fixtures to fix the part during the measurement process to ensure the accuracy and consistency of the measurement. In addition, functional testing is essential to evaluate the mechanical properties and performance of LSR parts. Compression, tension or elongation tests help evaluate material strength, while leak or pressure tests are used for sealing components. For parts with complex geometries or internal defects, advanced technologies such as X-ray or CT scanning can provide in-depth analysis to ensure the integrity of the entire part.
Eliminate defects with precise temperature control
During the LSR injection molding process, precise temperature control is critical to ensure consistent material properties. Fluctuations in mold or material temperature can cause defects such as warping, incomplete curing, or poor surface finish. Elimold uses advanced temperature monitoring technology to ensure stable temperatures throughout the molding process. By controlling temperature changes, the integrity and performance of LSR parts can be protected, ensuring part quality in demanding applications.
Contact Elimold today to discuss your project
Not sure which LSR production method is right for your part? Our engineers will evaluate and guide you to the best solution early in the design phase.
What is LSR Molding?
Liquid silicone rubber (LSR) injection molding, also known as liquid injection molding (LIM), is a thermosetting process that mixes two compounds together. This two-component compound is cured by heating in a mold with a catalyst to form a complete molded part. The production process of liquid silicone rubber (LSR) parts is similar to plastic injection molding, using the injection molding process. However, the main difference between the two processes is that LSR requires a cooled material delivery system and the mold needs to be heated. Liquid silicone rubber injection molding differs from the plastic injection molding process in that the core of LSR injection molding is mechanical mixing rather than pressurized impact mixing.
Liquid silicone rubber crosslinks through a platinum-catalyzed reaction. After curing, LSR cannot be re-molded or repurposed because of the high energy required to break down the crosslinked material. The structure of LSR makes it suitable for a wide range of temperatures, and the bonding between silicon atoms and oxygen atoms means that the polymer is not easily degraded. One of the main advantages of liquid silicone rubber is its chemical inertness or purity. Coupled with its ability to withstand sterilization processes, this makes LSR an ideal choice for many medical uses. Most liquid injection molding (LIM) processes are based on the many properties of liquid silicone. Liquid silicone rubber has high heat resistance, high tensile strength and flexibility. LSR also has excellent moldability and the finished product can be colored or transparent. Depending on the specific compound composition, liquid silicone can also be used as an excellent insulator or conductor.
How Does Liquid Silicone Rubber Injection Molding Work?
First, a liquid silicone rubber molding tool is created using CNC machining. The tool must be a high temperature resistant tool to withstand the LSR injection molding process. The tool can then be polished to allow for different surface finish options. Next, the completed tool is loaded into an LSR-specific injection molding machine that is precision tuned to accurately control the injection volume to produce the most consistent LSR parts. Materials used include standard silicones and specific grades to suit different part applications. Since LSR is a thermosetting polymer, its molded state is permanent. Unlike thermoplastics, they cannot be melted again. Once the LSR injection mold parts are ready, they can be removed from the mold and then used as prototypes or production parts.
Why use LSR injection molding?
Professional LSR injection molding provides clean, consistent results with tight tolerances that are difficult to achieve with alternative methods such as compression or transfer molding. One important advantage of LSR over gum-based molding silicone materials is its fast molding cycle. Depending on the stimulus and the cross-sectional area of the part to be welded, the welding cycle for LSR parts can range from 30 seconds to 3 minutes – our typical cure time is 25 to 50 seconds. In contrast, gum-based silicone in a traditional silicone mold may require a complete cycle time of 3 to 5 minutes. As a result, single- or dual-cavity injection molds will produce more parts than multi-cavity molds. Because fewer cavities are required to maintain production, tooling costs, lead times, and part costs are reduced.
Material Options for Liquid Silicone Rubber Injection Molding
Our liquid silicone rubber injection molding process offers a wide range of high-performance materials that can be custom to meet your application needs. We offer a variety of silicone rubber grades, and our team of experts will guide you in selecting the ideal material to ensure your part achieves the desired performance, aesthetics, and functionality to make your project a success from prototype to production.
- Standard Silicone: Available in 30, 40, 50, 60, and 70 durometers, providing a range of durometer options to suit different applications.
- Medical Grade Silicone: Biocompatible material for medical devices and implants, ensuring safety and reliability.
- Optical Grade Silicone: Transparent material ideal for optical applications, with excellent clarity and light transmittance.
- Fluorosilicone: Resistant to fuels and oils, ideal for applications requiring chemical resistance and durability.
Available Colors for Liquid Silicone Molded Parts
While the vast majority of molded parts are requested in standard white or clear. In addition, 20 additional colors are available, including various shades of black, blue, green, red, and yellow. Please contact us for a color stock sheet (PDF) listing the existing pigments available without a color matching charge. Silicone samples may also be available for some pigments. Custom colors can be developed. However, the additional hardware costs to support custom colors may exceed $3,500.
Advanced Materials Lab
If you are looking for a reliable design-to-molding manufacturing resource for your custom LSR project, our company is here to serve you. We can provide unique properties to meet your project needs. The experts in our Advanced Materials Lab can help you make the right material selection. Our material scientists are well versed in a variety of platinum-cured silicones and peroxide-cured silicones. Our material scientists will help you determine if a material that meets the specification requirements is the best choice for the application, or if selecting a different material that does not meet the specification will provide higher quality, reliability and performance for the final product.
Biocompatible Materials
Elimold has been at the forefront of advanced liquid silicone rubber molding technology. Our technicians use their deep knowledge and experience in liquid silicone rubber (LSR) molding to provide materials that are strong, durable, flexible and able to withstand harsh operating conditions. After extensive testing, liquid silicone rubber has demonstrated excellent compatibility with human tissue and fluids. Compared to other elastomers, liquid silicone rubber is resistant to bacterial growth and will not contaminate or corrode other materials. LSR is tasteless and odorless and can be formulated to strict FDA requirements. The material can be sterilized by a variety of methods, including steam autoclave, ethylene oxide (ETO), gamma irradiation, electron beam, and many other technologies.
Material Alternatives
By using alternative processes and materials, silicone-like parts can be manufactured without using liquid silicone injection molding. From a process point of view, the closest alternatives are injection molding thermoplastic elastomers (TPE) or thermoplastic vulcanizates (TPV): they are flexible, impact-resistant plastics that can be melted, injected and cured like other thermoplastics. The advantage of these materials is that metering and mixing are not required. However, despite their elastomeric properties, TPE and TPV also have the weaknesses of thermoplastics, such as degradation in sunlight, and may therefore not be suitable for certain medical applications. In addition to injection molding, TPE is one of the few materials that can be made into flexible 3D printing filaments: this material is used in the additive manufacturing of rubber-like parts. TPU is another such material.
Surface Finish Options
- PM-F0: Non-cosmetic, finish to factory discretion
- PM-F1: Low-cosmetic, most toolmarks removed
- PM-F2: Non-cosmetic, EDM permissible
- SPI-C1: 600 grit stone, 10-12 Ra
- PM-T1: SPI-C1 + light bead blast
- PM-T2: SPI-C1 + medium bead blast
- SPI-B1: 600 grit paper, 2-3 Ra
- SPI-A2: Grade #2 diamond buff, 1-2 Ra
Finish Options for Molded Parts
If the finish you want is not listed, please contact us and we will customize the finish for you individually.
Standard Finish
Moldmaker’s choice of finish, typically SPI B-2, with interior non-cosmetic faces left as-machined.
SPI Finishes
Range from Grade 3 diamond/high polish to 320 stone low polish, including SPI A-1 to SPI D-3 finishes.
As Molded
No secondary polishing or grinding, with parts showing tooling marks.
MoldTech Finishes
Include matte, swirls, lines, and patterns, with standard finishes such as MoldTech MT11010, MT11020, and MT11030.
Other Textures - VDI
VDI 3400 Surface Finish, processed mainly by EDM machining, produces fine to coarse matte finishes.
Assembly
Capability to assemble and label injection molded parts, with specific needs discussed with your salesperson.
Threaded Inserts
Installation of standard inserts in UNF and metric sizes.
Pad Printing
Transfer a 2D image onto a 3D part, subject to image review.
Laser Engraving
Engraving of part numbers, logos, and more onto your parts.
Industries We Serve
We have manufactured millions of parts for a wide range of applications and have expertise in a wide range of industry sectors. Our deep knowledge in these areas enables us to provide high-quality, tailor-made solutions for every project.
Parts and Applications
- Baby bottle nipples
- Pacifiers
- Medical masks
- Seals and gaskets
- O-rings
- Valve diaphragms
- Catheter tips
- Medical tubing connectors
- Respiratory masks
- Keyboard covers
- Smartphone gaskets
- Wearable device straps
- Electrical connector boots
- Cable grommets
- Pump diaphragms
- Hearing aid ear tips
- Sports mouthguards
- Breast pump parts
- Face mask straps
- Medical device housings
- Syringe plungers
- Dental appliance components
- Baby teething toys
- Medical suction bulbs
- Keyboard keypads
- Insulation bushings
- Waterproof seals
- Goggle gaskets
- Diving mask skirts
- Baby feeding spoons
- Medical vial stoppers
- Inhaler gaskets
- Food storage lid seals
- Smartwatch straps
- Heart valve components
- Insulin pump gaskets
- Breathing tube gaskets
- IV catheter grommets
- Medical sensor covers
- Keyboard dome switches
Expert Custom LSR Parts Supplier
Our customers span a wide range of demanding markets and companies of all sizes. As always, your engineering team has quick and easy access to our technical team to ensure your custom LSR part project goes smoothly. Customers working with us on prototypes have access to our new state-of-the-art Innovation Center, which produces production-ready prototypes at unparalleled speed. With our Innovation Center, prototype projects that used to take months to complete can now be completed in just days. We will compound, mix, design, and manufacture your most challenging custom LSR parts. Whether it’s a turnkey multi-color LSR injection molded part requiring multi-million dollar tooling, a complex LSR overmolded part, or a medical silicone part, we have the resources and deep expertise to help you complete your most challenging projects.
LSR Parts Manufacturer with Great Customer Service
Our capabilities, flexibility and customer service are reflected in every part we produce. We are an international manufacturer that provides parts sourced and manufactured in China, thus alleviating the supply chain issues that international suppliers often encounter. Our engineering team develops innovative solutions and has been trusted by customers for many years. We also have an attentive and responsive support team that provides excellent customer service and one-on-one support. We want to save our customers valuable time and resources as much as possible. We are happy to support you from the initial product idea to the final finished product. Our extensive service portfolio begins with joint product development, followed by prototype mold manufacturing using a number of different processes depending on your time and quantity needs, and finally the production of silicone parts in a regular production environment or clean room. All services follow strict quality standards and are continuously monitored by our comprehensive quality management system.
More Molding Service Options
With the different types of molding services we offer, you can find a manufacturing process that meets your project requirements. Below are a number of different thermoplastic molding manufacturing services that Elimold can provide.
Injection Molding
Overmolding
Gas Assist Injection Molding
Insert Molding
Structural Foam Molding
Micro Molding
Request Your Free Liquid Silicone Rubber(LSR) Injection Molding Quote Today
After receiving your drawings, our engineers will analyze your custom Liquid Silicone Rubber(LSR) Injection Molding parts right away. We actively work with you to clarify all details before providing a quote that is both economical and accurate.