Automotive 3D Printing
Improve manufacturing agility at every stage of the vehicle lifecycle with a flexible digital parts manufacturing platform. 3D printing is incredibly scalable in the automotive industry, and both single parts suppliers and industry-leading OEMs can benefit directly from using Elimold 3D printers. Elimold’s manufacturing platform offers a wide range of high-quality, durable materials.
Meeting the challenges of rapid innovation in today’s automotive industry
New mobility solutions and ecosystems are redefining the automotive industry and making rapid innovation critical. Our services in automotive engineering and additive manufacturing technologies for automotive parts can give you the competitive advantage you need to meet this challenge. We’ll help you increase manufacturing efficiency, reduce costs, and develop new designs to optimize performance and create the unique experiences your customers demand.
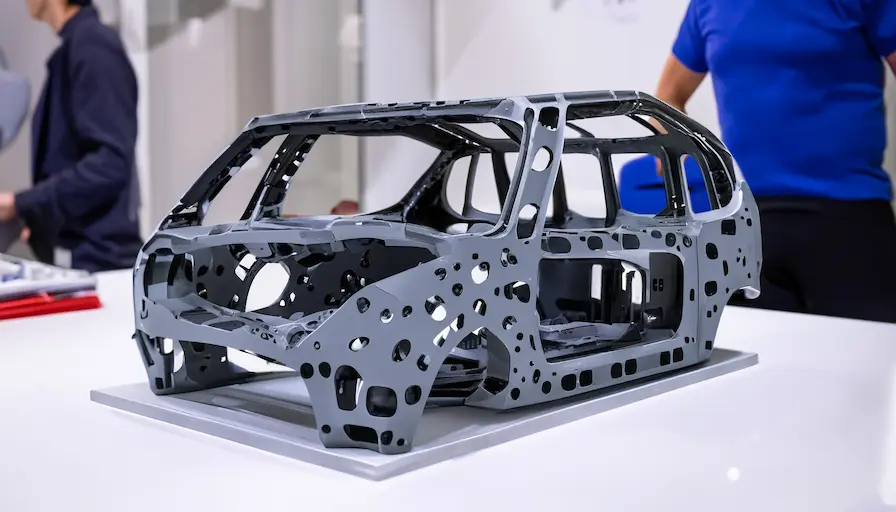
High-Quality Automotive 3D Printing Services
Elimold sets the standard for cutting-edge, high-quality automotive 3D printing services to meet the needs of the professional and commercial automotive sectors. With a team built specifically for the automotive industry, we are ready to tackle the most stringent regulations and custom parts with demanding requirements. Whether you need precision automotive part prototypes or production-grade components and materials, we provide on-demand automotive 3D printing solutions and technical support to ensure your project stays ahead of the curve.
Our in-house facility is equipped with state-of-the-art equipment: commercial and industrial-grade 3D printers for a wide range of technologies, ensuring your projects in the automotive sector benefit from precision, reliability and innovation.
As your trusted partner, Elimold is the first choice for high-precision custom automotive 3D printed parts designed for professional and commercial use. Upload your CAD file to get a custom quote and delivery time, and we simplify the process for your convenience.
Streamline your automotive manufacturing workflow with industrial 3D printing
In the high-demand, competitive automotive industry, keeping up with the pace of innovation can mean the difference between success and failure. With industrial 3D printing, you can streamline production by bringing manufacturing in-house quickly, on demand, and fully on-demand. Custom automotive parts without bottlenecks by eliminating third-party supply chains. Streamline prototyping with an affordable, hands-off process that enables efficient product iteration and designer creativity. Power automotive manufacturing from the drawing table to the assembly line with Elimold’s proven industrial solutions. Modernize your production today. Our experienced team of engineers and designers work closely with automotive customers to custom 3D printed parts to their specific needs. Whether it’s a prototype for a new product, a replacement part for an existing vehicle, or a component for a specialized vehicle application, we have the expertise to get the job done.
Explore Automotive 3D Printing Solutions
Our team can help you solve your most difficult design and production challenges with additive manufacturing solutions. Together we’ll identify your needs, work with you to optimize your design, prototype, validate, and define your manufacturing process.
Rapid Prototyping
We can quickly produce 3D printed prototypes of automotive parts, allowing customers to test and improve their designs before full production.
Production Parts
We specialize in 3D printed automotive production parts to reduce lead times, eliminate injection mold investments, iterate quickly, and allow for design freedom and part consolidation.
Custom Part Production
Our team can design and produce custom 3D printed parts for a variety of automotive applications, including interior components, exterior parts, and even engine components.
Replacement Part Production
We can create 3D printed replacement parts for older or hard-to-find automotive parts, ensuring our customers’ vehicles run smoothly.
Tooling and Fixtures
Our 3D printing services can also be used to produce tooling and fixtures for automotive manufacturing processes, increasing efficiency and reducing costs.
Accelerate mold production
3D printing helps automotive companies control mold equipment production from end to end without investing additional resources. In addition, this disruptive technology helps manufacturers reduce delivery time to less than one week.
3D Printing Processes for Automotive Applications
Accelerate automotive product development with 3D printing of rapid prototypes and low-volume production parts for traditional, electric, and autonomous vehicles.Whether you’re a small shop or a large automotive company, Elimold has the experience, equipment, and capabilities to meet your automotive 3D printing and additive manufacturing (AM) needs.
Direct metal laser sintering (DMLS)
Stereolithography (SLA)
Selective Laser Sintering(SLS)
PolyJet
Multi Jet Fusion (MJF)
Digital Light synthesis(DLS)
Fused DepositionModeling (FDM)
P3 technology (DLP)
Solidscape (wax deposition)
The potential of additive manufacturing for series-produced vehicles
3D printing technology has the potential to optimize the automotive production value chain and to respond quickly and flexibly to new trends. In the automotive industry, where car manufacturers, OEMs and tool suppliers are under high cost and innovation pressure, this potential is extremely valuable.
- Individual and revolutionary: series custom and design
- Efficient and high-performance: optimized components
- Sustainable and cost-effective: spare parts on demand
- Flexible and functionally integrated: tool manufacturing by 3D printing
Taking Automotive R&D to the Next Level
The automotive industry has benefited greatly from the integration of 3D printing technology and the increased speed of R&D. Automotive 3D printing, or additive manufacturing, enables rapid prototyping, allowing automakers to design, test, and improve parts faster than with traditional manufacturing methods.
Innovation thrives when automotive part designers and engineers can focus on improving designs rather than waiting for prototype production. With 3D printing in the automotive industry, high-fidelity prototypes can be produced in just a few hours, significantly reducing the time spent waiting to get a tangible version of a design. This fast turnaround not only streamlines the development process, but also promotes a more dynamic and efficient approach to automotive design, allowing for real-time iteration and improvement.
Accelerate automotive breakthroughs with industrial 3D printing
Time
Automotive additive manufacturing production processes can reduce the time it takes to build a part by up to 75% by eliminating the need for tool or mold making. This is true for product development for model and prototype manufacturing, the production of small and medium series or the manufacture of complex or variant-rich parts.
Costs
Complex geometries, structures and surfaces as well as precisely fitting components: Due to the high costs of tool manufacturing, conventional processes quickly reach their economic limits. One of the biggest advantages of additive manufacturing in the automotive industry is the economic benefits – both for individual components and series assemblies.
Weight
3D printing enables geometric freedom in automotive manufacturing. Even the most complex lightweight designs and topology-optimized or generatively designed components can be easily realized. Vehicles become lighter, fuel consumption decreases and the design options become more diverse.
Solutions to solve automotive challenges
Whether you need high-precision parts at scale or tough thermoplastics that replicate automotive-grade production plastics, our additive manufacturing technologies can help you design, test, and iterate components quickly and efficiently. Reduce the time it takes to produce high-performance automotive parts from days or weeks to hours.
Accelerate automotive innovation
While new technologies create exciting opportunities, they also present tough engineering challenges. With a wide range of advanced materials and additive technologies, increased ability to test and iterate, and greater production flexibility, our additive technologies make it easier to develop cutting-edge 3D automotive parts for performance mobility innovation.
Leverage our automotive and additive expertise
Our team offers more than just products, we provide a comprehensive portfolio of solutions with the experience and expertise to help you solve automotive problems and create value efficiently and effectively. We can help you use our additive technologies to improve the driving experience and increase productivity in a variety of ways.
Advantages of Additive Manufacturing for Automotive
- Lightweight custom designs with excellent strength-to-weight ratio
- Reduce material weight and improve fuel efficiency
- Parts consolidation and inventory reduction
- Reduce tooling and mold design for complex parts
- Complex parts with fast turnaround time
- Significant cost reduction
- Improve part performance
- Enable just-in-time, distributed manufacturing and production
- Reduce supply chain costs with additive manufacturing
Vehicle prototyping and custom through additive manufacturing technology
The automotive industry is known for being engineering-intensive and demanding, and 3D printing technology is revolutionizing the way cars are designed and manufactured, helping automotive companies reshape supply chains and production lines. 3D printing allows for faster prototyping, customization, and on-demand production. It allows complex parts to be designed and produced without expensive tools or molds, which greatly reduces manufacturing time and costs.
3D printing promotes lightweight design by optimizing materials and structures, thereby improving the fuel efficiency and performance of vehicles. It promotes the sustainable development of the automotive industry by reducing waste and the need for large inventories for just-in-time production. As global automotive companies continue to adopt 3D printing technology to produce automotive parts, it will bring more innovative designs, faster production cycles, and more personalized and efficient vehicles. If you need custom auto parts, you can use Elimold’s 3D printing services.
Enhanced Prototyping
The ability to quickly prototype is critical in automotive design. 3D printing enables engineers and designers to turn digital models into physical parts in hours, a process that would normally take weeks or even months to manufacture using traditional processes. 3D printing accelerates the prototyping phase, allowing multiple iterations to be made quickly and inexpensively. This flexibility allows designers to experiment with complex designs and geometries that are difficult or impossible to achieve using traditional manufacturing techniques. Using materials that mimic the properties of production-level components, 3D printed prototypes can be functionally tested under real-world conditions. This helps uncover potential design flaws before going into mass production.
Custom Components and Personalization
Demand for custom is on the rise in the automotive industry, with consumers seeking unique features that set them apart from standard models. 3D printing meets this demand by producing custom parts at a relatively low cost. Whether it’s a luxury vehicle or a modified car, 3D printing can produce parts that are custom for a specific vehicle or customer preference. This includes everything from custom interior elements to specialized vehicle enhancements. For high-performance vehicles or limited edition models, manufacturers can use 3D printing to produce small quantities of parts more economically than traditional manufacturing, which often requires expensive molds and setups.
Production of End-Use Parts
Elimold’s 3D printing services enable the production of end-use parts for the automotive industry. Not just for prototypes or custom parts, but also for the production of components that are integral to the daily operation of a vehicle. 3D printing can combine multiple parts into a more complex assembly. This reduces assembly time and can improve part strength and weight, both of which are critical factors in automotive design. With advances in printable materials, including high-strength alloys and advanced composites, 3D printed parts are increasingly meeting or even exceeding the performance requirements of traditional manufacturing methods. Additive manufacturing is inherently less wasteful than subtractive manufacturing methods because it only uses the material needed to make the part. This helps achieve sustainability, which is becoming a key selling point in the automotive industry.
Why do companies in the automotive industry use Elimold?
As industry trends such as autonomous driving, in-vehicle connectivity and hybrid/electric vehicles continue to drive innovation, agility-focused automotive companies are turning to Elimold to accelerate new product development and get to market faster. Our diverse 3D printing technologies can support customers in the automotive industry:
- Design for Manufacturability (DFM) feedback for every quote
- Quality checks to verify part geometry and FAI reporting
- Ability to 3D print functional prototypes using a variety of material options suitable for testing
- Diverse material and process options help reduce component weight
Easing Challenges in the Automotive Industry
Automobiles are a creative and challenging field where industrial design and mechanical arts play a vital role. Manufacturers must strive to produce lightweight, durable parts at a low cost. In addition, ensuring the strength and efficiency of the product also brings new challenges. At Elimold, we use advanced 3D printers to create functional prototypes and finished parts with complex geometries. We help manufacturing companies that cannot mass produce one-off parts with additive manufacturing. Any 3D printed automotive part in a vehicle can be custom through additive manufacturing.
3D printing technology can produce automotive parts with unique designs that were previously impossible. Therefore, we can meet the design and production challenges that come with the automotive industry. Elimold is committed to helping the automotive industry grow by providing hassle-free and innovative 3D printing solutions. We have a team of skilled professionals who can meet any automotive industry challenge. With our advanced 3D printing applications in the automotive industry, we can help you create prototypes, production parts, and molds. In addition to this, we also provide customers with custom solutions that suit their specific needs. Experience the best customization with the support of our more than 45 industrial-grade 3D printing materials.
Industrial 3D printing and custom
Various applications required by the automotive industry can be custom with industrial 3D printing and delivered quickly.
- Design freedom for individual adaptations
- Short production times, delivery within a few weeks
- Part quality, functionality and safety meet MINI’s strict product guidelines
- System tailored for series production
Metal 3D Printing Automotive Industry Parts Molds
Using metal 3D printing to make molds for automotive parts can save time and money. Therefore, it is crucial to use the right additive manufacturing process as well as the right materials. Tools are generally instruments or components used to create geometric shapes in various production processes. These production processes include injection molding, die casting, cutting, stamping, extrusion and assembly. Typical categories of machine tool tools include fixtures, clamps, gauges, molds, dies, cutting equipment and patterns. Usually, mold parts are produced in relatively small quantities, so the cost is high. And the process of making tools is time-consuming and expensive. Complex geometries, high precision and surface finish requirements, combined with hard and wear-resistant materials, place high demands on highly qualified labor and equipment. In-house metal 3D printing enables faster and cheaper mold production. Using metal 3D printed tools means you can move faster, increase productivity and improve the functionality of the tools. Being able to significantly reduce delivery time is a major advantage.
Material Options
Elimold’s 3D printing technology offers a variety of materials to meet the needs of various automotive applications. These include engineering-grade high-performance thermoplastics, nylon polymers, and high-strength metal materials.
- Aluminum
- Stainless Steel
- Titanium
- Inconel
- Cobalt Chrome
- Copper
- Maraging Steel
- Nickel Alloy
- More
- ABS
- Polycarbonate
- Polypropylene
- Nylons
- TPU
- Elastomer
- Carbon Fiber
- PETG
- More
Finishing options
At Elimold, our Automotive 3D-printed parts can be finished in various options. Our finishing solutions for additive manufacturing include:
- Standard
- Media blasting
- Polishing
- Sanding
- Brushing
- Painting
- Silk printing
- Plating
- Texturing
3D Printing Applications for the Automotive Industry
When you need to, 3D printing allows you to respond faster when OEMs and suppliers make engineering changes. You can create prototypes and placeholder parts with more iterations and faster time to market.
In-house 3D printing also allows you to work more closely with operators. Collaboratively design and optimize custom tooling to improve assembly station ergonomics and increase their satisfaction and productivity. Some of the world’s largest automotive companies leverage 3D printing to gain cost efficiencies during the design iteration phase. End-use production components include everything from custom seats to car brackets to fuel injectors. Common automotive parts we can manufacture include:
- Sprockets
- Enclosures and housings
- Fan blades
- Gears, latches, and brackets
- Engine parts, manifolds, and heat exchangers
- Hose and wire clips
- Washer fluid and fuel caps
- Fixtures
- Assembly line components
- Plastic dash components
- Dashboards
- Center consoles
- Headliners
- Glove boxes
- Door Panels, trim, pockets
- Speaker panels
- Vents
- Steering wheels
- Customized aftermarket parts
- Lenses and lighting features
Current applications and future prospects of additive manufacturing in the automotive industry
The automotive industry has always been at the forefront when it comes to implementing new technologies. Assembly line operations and the use of industrial robots play an important role in terms of precision and efficiency in vehicle assembly. Additive manufacturing of automotive components helps to increase the flexibility, agility and resource efficiency of modern production lines. Although Elimold’s automotive 3D printing systems are not yet ready for production of complete vehicles, many automotive components are already additively manufactured today. This is mainly due to increased customer demand, stricter environmental regulations in terms of sustainability, alternative powertrains and personalization. This requires a technology that can produce prototypes quickly and shorten product development cycles. Complex components must be mass-produced in an economical manner. 3D printing for automotive applications is the solution.
Contact us to start your journey of 3D printing of auto parts
If you are an automobile manufacturer or related supplier, Elimold will provide you with professional 3D printing solutions. With advanced 3D printing technology and rich experience, we can provide you with custom automotive parts and interior manufacturing services. Please contact our team to tell us your needs and we will provide you with the best solution. Click the button below to send us an inquiry today, we look forward to adding new value to your automotive project!