The high-gloss injection molding technology is also known as the rapid thermal cycle injection molding technology. The application of this technology can copy all the appearance of the mold surface very well so that the surface of the product part has no melting marks, and the surface high-gloss can achieve the actual effect of mirror glass, improve the compressive strength of plastic parts and surface strength; make thick-walled forming to improve the fluidity of injection molding, improve product quality and compressive strength; reduce the injection cycle time of thick-walled tube forming by more than 60%; no need to post-air pollution is more serious in the painting process, which can reduce the production process, save energy and raw materials. Immediately reduce the cost of plastic products, protect the ecological environment and the personal safety and physical and mental health of the current operating staff.
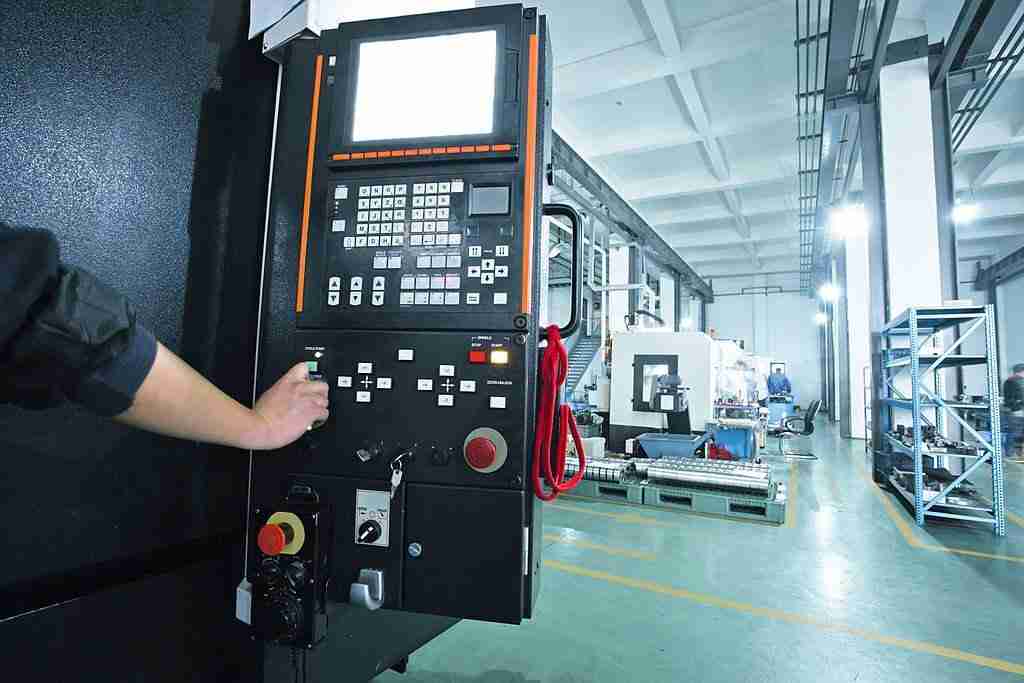
When doing high-gloss injection molding, what must be paid attention to?
01 The oil heater mold with high-temperature oil heat conduction is designed with a symmetrical heating or cooling pipeline. According to the oil heating system software, the mold heating function is achieved, and at the same time, it has the effect of cooling the whole injection process. The temperature can reach 350°C. Because the thermal conductivity of oil is low, the efficiency is low, and the resulting gas damages the high-gloss forming quality, but the actual effect is less ideal. But at this stage, the company’s oil heaters are more extensive and have rich application experience.
02Ultra-high pressure water heat conduction high-pressure mold temperature machine The internal design of the mold is balanced, and water of different temperatures is used in different links. When heating, it enters high-temperature superheated water, and when cooling, it is converted into low-temperature cooling circulating water to complete the heating or cooling of the mold surface. If the water is pressurized, the temperature can reach 140-180 °C, and the temperature can be increased rapidly.
03 The basic principle of the steam oil temperature machine with steam heat conduction is similar to that of the high-pressure mold temperature machine. The balanced pipeline inside the mold is designed to enter the steam during heating and convert to low-temperature water during cooling to complete the heating or cooling of the mold surface (steam heating Generally, the pipeline must be dried with air compression). The ultra-high pressure steam heating system software can make the mold surface temperature reach 160℃. Because the vapor is a relatively strong electrolyte, its specific heat is small, and the relative warming time is relatively long. To achieve 150 ℃, the mold surface temperature must be around 300 ℃ steam. However, because the steam cannot be recycled in the production process, boilers and pipelines must be installed, resulting in high operating costs.
04 The electric heating oil temperature machine with heat conduction of heating tube adopts resistor heating components (insulation board, electric heating frame, electric heating ring, etc.) (including stainless steel plates and copper pipes), spiral electric heating alloy wires (nickel-chromium alloy, iron-nickel-iron alloy) are evenly distributed along the radial direction of the management center in the pipe. The gap is filled with magnesia sand with excellent heat transfer performance of the insulating layer, and both sides of the branch pipe are sealed with silicone. Electrothermal materials can heat gases, solids, and various liquids. At this stage, the heating system software cost of the electric water heater immediately modified in the mold is relatively high, and the annual patent fee for the mold design scheme needs to be paid. The heating rate of the heating tube is fast, and the operating temperature range can reach 350 °C. After using the system software, the mold temperature can be heated to 300 °C in 15 seconds, and then the mold temperature can be cooled to 20 °C in 15 seconds. But it is only suitable for small-sized commodity applications. Because the heating wire is immediately heated at a higher temperature, the relative die life will be reduced.
05 The magnetic effect heating system software of high-frequency current increases the temperature of the product workpiece according to the basic principle of the magnetic effect of the current. Because of the skin effect, the vortices created on the product workpiece’s surface are strong but weaker on the inside, approaching zero at the core. Therefore, this method can only heat the surface of the product workpiece to the deep layer of the skin, so the heating body is small, the heating speed is faster, and the heating rate is above 14℃/s. The rate has long been above 20°C/s. After the surface heating is carried out, it can be matched with rapid low-temperature freezing equipment to achieve the actual effect of rapid heating and cooling of the mold surface and complete the control of variable mold temperature.
06 Infrared induction radiation source heating system software scientific research staff are comprehensively using the infrared induction radiation source method to heat the die position immediately. The heat conduction method of infrared induction is the heat conduction of the radiation source, and radio waves transmit the kinetic energy without needing a heat transfer medium. It has a certain ability to work through. Compared with other methods, it has the advantages of energy saving, safety, simplicity of machinery and equipment, and easy promotion. However, the heating speed is relatively slow due to the poor infrared induction absorption of bright metal materials.
07 The high-temperature vapor of the vapor-type receipt table system software is used as a substance that rapidly changes the mold temperature. Before the filling process, the vapor is quickly and precisely introduced into the die, which can instantly increase the mold surface temperature to around 200 °C. The high-temperature area can be operated around the surface of the mold, and it is not easy to cause the mold’s other parts to increase the mold’s size due to the strong temperature. The technology does not need to make great changes to the current mold, the mold manufacturing cost is low, but the tightness requirements are high.
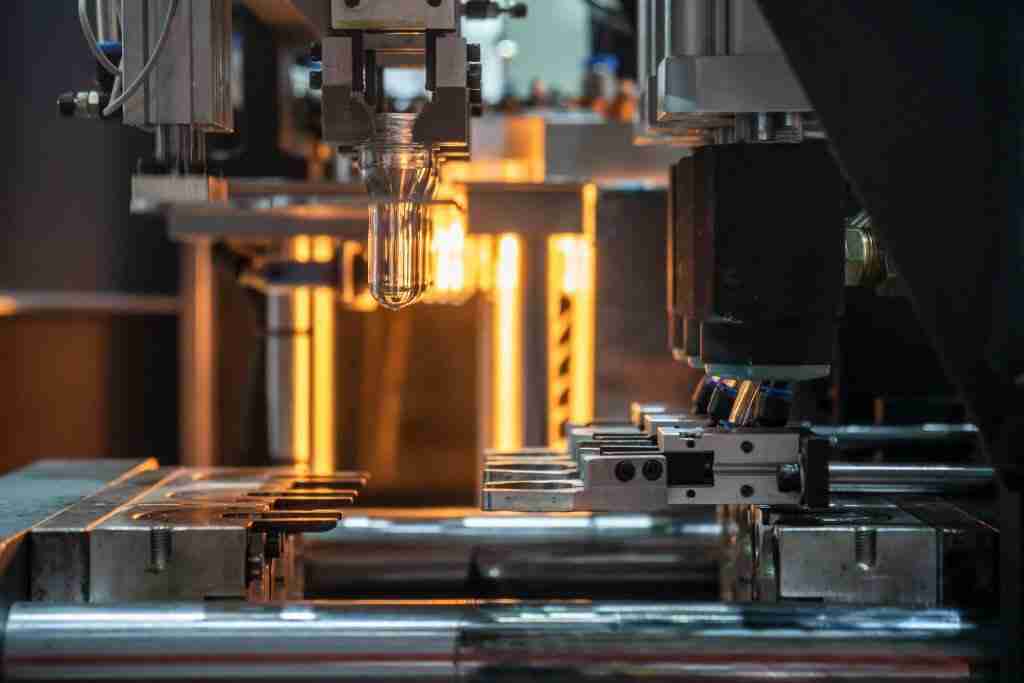
At this stage, some problems in the automatic temperature control system must be dealt with:
- There are a few easy-to-use heating methods; the more successful ones are steam and high-temperature water heating.
- High-gloss injection molding adopts an independent mold temperature automatic control system, which must be used with the injection molding machine.
- The cost of machinery, equipment, and operation increased.
How to enable the variable mold temperature control system to carry out economic development and large-scale production without compromising the molding cycle time is a problem that everyone is competing for development trends and improvements. Further scientific research, development, and design must be carried out in easy-to-use, low-cost, and rapid heating methods and integrated high-gloss injection molding machines.
High-gloss injection molding is a more general name for injection molding companies at this stage. From the perspective of the gloss of injection molded products, because the temperature of the page where the front of the melt fluidity is in contact with the mold surface is increased, it is very easy to copy the subtle appearance of a part of the mold, such as High-gloss molds and rubber products can produce high-gloss injection molding products, and complete one-step injection molding to achieve successful products, so it is called high-gloss injection molding, and its full name should be variable mold temperature injection molding for high-gloss products.
In addition, there are many other names, such as the process that adopts rapid heating and cooling, which is called rapid thermal cycle injection molding (RHCM); from the perspective of mold temperature change, it is called variable mold temperature, dynamic mold temperature, and replacement heat and cooling. Mold temperature control system; from the perspective of post-treatment processes such as painting, it is called paint-free injection molding; from the perspective of surface defects, it is called non-melt joint and trace-free injection molding.
The heating method is also called steam type, electric heating type, boiling water type, high-temperature type, magnetic induction heating type, mold temperature control system, etc. From the perspective of mold temperature control equipment, it is also called a steam oil temperature machine, superheated water oil temperature machine, electric heating oil temperature machine, mold temperature machine, oil heater, electric current magnetic effect oil temperature machine, etc.
For more injection molding technology experience sharing, please pay attention to Lixin Plastic Co., Ltd. and discuss with you. Welcome to contact Elimold.