In the processing industry, the order of operations is very important which is related to the quality assurance of products. And it will be easy to cause great losses if one order is wrong. The more serious is that the parts must be re-processed, and the products which are processed first will be scrapped, and precision machining is one of them, so what is its order?
First, The arrangement of the precision machining sequence should be considered according to the structure of the part and the condition of the blank, and the need for positioning and clamping. The key point is that the rigidity of the workpiece is not damaged.
(1)The processing of the previous process cannot affect the positioning and clamping of the next process, and general precision machining processes interspersed in the middle should also be considered comprehensively.
(2)The inner shape and cavity machining process is performed first, and then is the outer shape machining process.
(3)It is best to connect the same positioning, clamping method, or tool processing process to reduce the number of repeated positioning, tool changes, and moving of the platen/fixture.
(4)For multiple processes carried out in the same installation, the process with little damage to the rigidity of the workpiece should be arranged first.
Second, a method of centrally classifying tool operations is to divide the process according to the tools used and use the same tool to process all the parts that can be completed. Use the second and third knives to complete other parts that they can complete, which can reduce the number of tool changes, compress the idle time, and reduce unnecessary positioning errors.
Third, For parts with many processing contents, the processing part can be divided according to their structural characteristics, such as inner shape, outer shape, curved surface or flat surface, etc. Generally, the plat and positioning surface is processed first, then machining the hole; The simple geometric shape is processed first, and then machining the complex geometric shape; The parts with lower precision are processed first, and then machining the parts with higher precision. The above is the machining process of precision parts. Follow these steps, which will greatly reduce your processing risk.
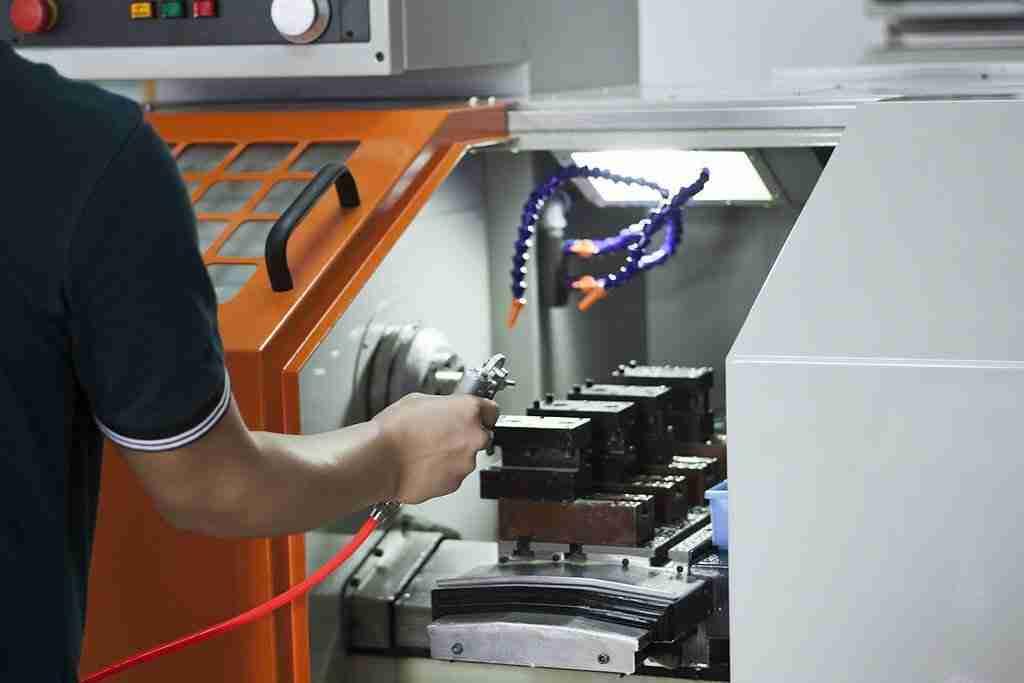
Technical requirements for precision machining
What are the technical requirements for machining mechanical parts?
Contouring of parts:
1. The unmarked shape tolerance shall meet the requirements of GB1184-80.
2. The allowable deviation of the unmarked length dimension is ±0.5mm.
3. No fillet radius R5.
4. The chamfering without the note is C2.
5, acute angle, blunt.
- The sharp edge is blunt, and the burr should be removed.
Part surface treatment:
1. The surface finish of the parts, which there should be no scratches, scratches, and other defects that damage the surface of the parts.
2. The surface of the processed thread cannot have defects such as black skin, bumps, random buckles, and burrs. All steel surfaces that need to be painted must be removed from rust, scale, grease, dust, mud, salt, and dirt before painting.
3. Before rust removal, use organic solvent, lye, emulsifier, steam, etc., to remove grease and dirt on the surface of steel parts.
4. The interval between the surface to be coated by shot peening or manual rust removal and the primer coating shall not be more than 6h.
5. The surfaces of the riveted parts in contact with each other must be coated with anti-rust paint with a thickness of 30-40 μm before connecting. Lap edges should be closed with paint, putty, or adhesive. Primer damaged due to processing or welding, to be repainted.
Heat treatment of parts:
1. After quenching and tempering treatment, HRC50~55.
2. Medium carbon steel: high-frequency quenching for 45 or 40Cr parts, tempering at 350-370℃, HRC40-45.
3. Carburizing depth 0.3mm.
4. High-temperature aging treatment.
Technical requirements for precision machining:
1. The finished parts should not be placed directly on the ground, and necessary support and protection measures should be taken.
2. The processing surface is not allowed to have rust, bumps, scratches, and other defects that affect performance, life, or appearance.
3. There should be no peeling on the surface of the rolling finishing.
4. There should be no oxide scale on the surface of the parts after heat treatment in the final process. Finished mating surfaces and tooth surfaces should not be annealed.
Sealing of parts:
1. Each seal must be soaked with oil before assembly.
2. Strictly check and remove the sharp corners, burrs, and foreign objects left in processing parts before assembly. Make sure that the seals are not scratched when they are installed.
3. After bonding, the excess adhesive that flows out should be removed.
Gear technical requirements:
1. After the gear is assembled, the contact spots and backlash of the tooth surface should meet the requirements of GB10095 and GB11365.
2. The datum end face of the gear (worm gear) and the shaft shoulder (or the end face of the positioning sleeve) should fit together, and the 0.05mm feeler gauge should be used for inspection. And the verticality requirements of the gear reference end face and the axis should be guaranteed.
3. The joint surface of the gearbox and the cover should be in good contact.
Machining process specification
For the technical specification of mechanical processing, the technicians determine the technical process to be adopted according to the number of products, equipment conditions, and the quality of workers and write the relevant content into a technical document called a technical specification.
To facilitate the preparation, execution, and production organization management of process regulations, it is necessary to divide the process into different levels of units. They are operations, installations, stations, steps, and passes. The process is the basic unit of the process.
The machining process of parts consists of several processes.
process
The part of the process that a worker (or a group of) workers continuously completes on a work site (or a machine tool) on one (or several simultaneously) workpieces is called a process. The basis for dividing the process is whether the work location changes and the work process is continuous.
For example: Machining a batch of shafts on a lathe can either rough and finish each shaft continuously or rough the entire batch and then finish them in sequence.
In the first case, the machining consists of only one process; in the second case, due to the interruption of the continuity of the machining process, although the machining is carried out on the same machine tool, it becomes two processes.
The process is the basic unit of the technological process and the basic unit of the production plan.
Install
In the machining process, the process of making the workpiece occupy a correct position on the machine tool or in the fixture and clamp is called clamping. Sometimes, the workpiece must go through several clampings on the machine tool to complete – the work content of one operation. The installation refers to the part of the process completed after the workpiece is clamped once
For example, machining a shaft on a lathe, first machining part of the surface from one end, then turning around and machining the other end, the process content at this time includes two installations.
Station
When using an indexing (or shifting) fixture, a rotary table, or processing on a multi-axis machine tool, after the workpiece is clamped once on the machine tool, it has to go through thousands of positions for processing. The part of the process completed at the location is called the station.
In simple terms, the part of the process completed by the workpiece relative to the machine tool or tool for each processing position is called a station.
work step
Under the condition that the machined surface, cutting tool, cutting speed, and feed rate remains unchanged, the part of the process that is completed continuously is called a step. It is also often called “feed” in production.
To improve productivity, several tools are used for simultaneous machining, and several steps for machining surfaces, called compound steps, can also be regarded as one step.
Tool path pattern (pass)
The part of the work step completed by the machining tool once on the machined surface is called a pass.
For example, if the metal layer is very thick for shaft parts, it must be cut several times. At this time, each cut is called a pass. Therefore, on the premise that the cutting speed and feed amount remain unchanged, the tool completes one feed movement called one pass.
Partner with Elimold
The above are the relevant processing skills and knowledge points summarized by the mechanics of Elimold enterprises. If you need CNC machining, our team of experts can talk you through your part design drawings and help you choose the best solution for your project. As a trusted CNC machining partner, Elimold also provides high-quality CNC machining capabilities through CNC machining equipment based on routers, lathes, drills, and milling machines. Contact us today to get started.
Visit our Resource Center to learn more about CNC machining, including tips for reducing costs and design best practices.