Overmolding is a unique injection molding process that seamlessly combines a variety of materials into a single part or product. It typically consists of a hard plastic-based part covered with a thin, flexible, rubber-like thermoplastic elastomer (TPE) or other material, using either single-injection (insert molding) or two-injection (multi-injection) injection molding techniques.
In short, overmolding is an injection molding process in which two or more materials combine wires and connectors to form a component.
An over-molded or over-molded cable is a complete assembly that combines the wire and connector into a seamless component. The cable assembly is placed in a mold. Next, the molten plastic material is injected into the mold cavity. Once the plastic material has cooled and cured, it will conform to the shape of the mold and encapsulate the connection point between the connector and the wire.
Overmolding is becoming increasingly popular with product manufacturers. Considering its significant advantages, you may find that overmolding is an excellent choice for your next project.
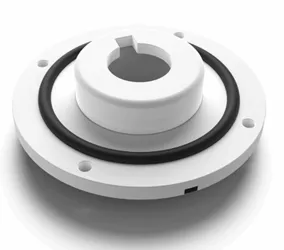
Why Overmolding?
Manufacturers who want to add a soft-touch appearance to their products to enhance grip or “feel” and provide a stylish look that appeals to consumers are prime candidates for overmolding. Overmolding can also extend product life by reducing shock and vibration, dampening sound, providing electrical insulation, and improving chemical/UV resistance. Overmolding also reduces production costs while improving product viability and customer satisfaction.
Advantages of using the overmolding process
All the advantages of overmolding boil down to longer life and reliability. Overmolding shields internal components and improves the quality of protection.
1. Better product performance
The main reason for overmolding to design and manufacture a product or part is to improve product performance.
TPE is an ideal material to provide a soft, non-slip grip for any number of products. The tactile feel of these products is not only comfortable but critical—medical products, such as surgical instruments.
In addition, TPE surfaces can act as an environmental barrier, protecting products and extending their shelf life by reducing shock, vibration, and noise – a key advantage of overmolding.
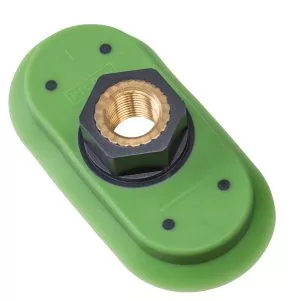
2. Reduced production costs
Secondary molding is rare because it adds value in many ways while reducing production costs.
How about this? Overmolding reduces the number of manufacturing steps. For example, in the automotive market, it eliminates injection molding and assembly of parts such as gaskets or bumpers, as well as secondary surface preparation operations (priming, painting, or coating).
Overmolding can be validated using 3D printing technology.
The design engineering of an overmolding mold is a task in itself. Design must be considered for any overmolding project, as errors can significantly impact production costs, cycle time, time to market, and overall product quality and performance, especially when designing multi-cavity molds and handling high rolls. Due to the increasing complexity and availability of prototyping technology, engineering teams can 3D print tools and test them for functionality and manufacturability before cutting them into steel. The ability to manufacture prototypes significantly reduces cost, time, and material waste. The right manufacturer can offer fully customized over-molded components, mass production, and quick turnaround.
How does the overmolding process work?
The following are three types of over-molding.
Clamp Molding
Insert molding is the best form of overmolding when molding soft elastomers or hard plastics. It is the best type because it is more economical and less difficult than the other types. In insert molding, the hard segment is first separated into the tool, then the soft material is ejected.
It also involves the use of elastomers as adhesives. This can be in the form of mechanical locks, chemicals, etc. The elastomer must be heated to a suitable temperature to achieve chemical bonding. This is necessary to heat the surface of the hard segment.
Secondary Forming
Unlike insert molding, overmolding requires the use of two injection molding machines. The hard segment is first injected into the elastomeric mold and then into the injection molding machine.
The heated substrate used is always in a semi-solid or gel state. The design of the mold can be modeled to project the lateral portions of the hard segment onto the substrate. For those who value a stable mechanical bond, the overmolding process is the right choice.
Co-injection
Of the three types of overmolding, co-injection molding is the most expensive and the most difficult to control. It is also a different process because it requires injecting the base material and the elastomer into the same mold. It also requires material compatibility.
In terms of quality, overmolding and co-injection molding are the best. This is because all materials are in the same molten state.
Overmolding applications
Overmolding is used in various industries, from consumer products to automotive and electronic components, but it is particularly well-suited for medical and healthcare applications. Devices that come into contact with, enter, or are inserted into the human body may have to meet stringent requirements and have challenging functions. They may have to be autoclavable, resistant to chemical exposure, and meet standards including FDA, USP Class VI, ISO 10993, and biocompatibility. In many cases, no one resin can meet all requirements. Multiple materials may have to work together almost seamlessly for safety and sterility, and over-molding excels in this area.
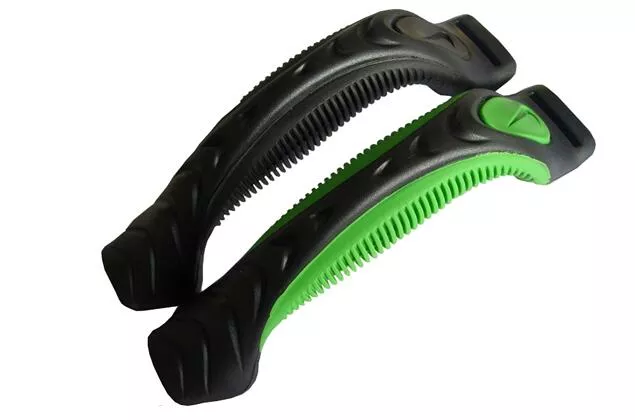
Automotive vibration damping
The overmolding process is well-suited for manufacturing products that are isolated from vibration. The rubber-like connection between one part and another eliminates vibration. This makes the process necessary for manufacturing motors and pumps.
Overmolding process for manufacturing comfort tools
Overmolding materials provide comfort due to better grip. This makes the process ideal for manufacturing products with better ergonomics. The molding process can take many shapes and be applied to almost any situation. That’s why it is ideal for overmolding bicycle handles or kitchen appliances.
Secondary molding process for waterproof products
Depending on the type of plastic used, overmolding is an excellent process for making waterproof products. This makes it suitable for the electronics world. This makes plastic overmolding an ideal waterproof alternative to traditional seals such as O-rings. Not only are they waterproof, but they can also be made flexible.
Making sound-absorbing products
Overmolding is the ideal process for making products that need to absorb sound waves. Making an enclosure that absorbs the sound of a motor is the right process to make a quieter device.
Use custom techniques for molding.
Are you ready to start molding but unsure if overmolding is the right choice? I trust the team of manufacturing experts at Elimold to advise you on the best fit for your product. Injection molding may be the solution you are looking for. Regarding low-volume foam or rapid prototyping, we also offer open-mold molding.